Spring steel and preparation method thereof
A spring steel and weight technology, applied in the field of spring steel, can solve the problems of low fatigue resistance, difficulty in grasping and realizing inclusion control, affecting fatigue performance, etc., and achieve good fatigue performance
- Summary
- Abstract
- Description
- Claims
- Application Information
AI Technical Summary
Problems solved by technology
Method used
Examples
preparation example Construction
[0041] According to the preparation method of the spring steel of the present invention, the method comprises that the spring steel raw material is subjected to preliminary refining, refining, cooling forming, rolling, quenching and tempering successively, wherein the composition of the spring steel raw material is such that the composition of the spring steel obtained is For, based on the total amount of the spring steel, the spring steel contains 0.56-0.64% by weight of C, 1.6-2% by weight of Si, 0.6-0.9% by weight of Mn, 0-0.015% by weight of Ti, 0.0055 - 0.03% by weight of S and 0.01-0.02% by weight of Als, the balance being Fe and unavoidable impurities, and the weight ratio of the S to the Als is 0.55-3, and the Als is acid-soluble aluminum.
[0042] Wherein, the method for preparing the spring steel of the present invention can adopt the existing process. For example, it can be carried out through the steps of primary smelting, refining, cooling forming, rolling, quench...
Embodiment 1-7
[0046] This example is used to illustrate the spring steel and its preparation method according to the present invention.
[0047] Put molten iron (the contents of various trace components: 3.74% by weight of C, 0.03% by weight of Si, 0.15% by weight of Mn, 0.083% by weight of P, and 0.016% by weight of S) into a 120-ton converter for primary smelting, blowing After 40 minutes of tapping, the tapping temperature is 1680°C. After tapping, adjust the composition of molten steel to the composition shown in Table 1 by adding pitch coke, ferrosilicon, ferromanganese, ferrochrome, and aluminum wire, and then add 840 kg of CaO containing 45% by weight, CaF 2 Refining slag of 10% by weight, refined at 1530-1555°C for 30 minutes, the refined molten steel was evacuated in RH vacuum device for 13 minutes (under the condition of vacuum degree less than 300Pa), and finally cast in 6 machines and 6 streams The 280×325mm slab was cast on the machine, and the cooling rate in the forced cooli...
PUM
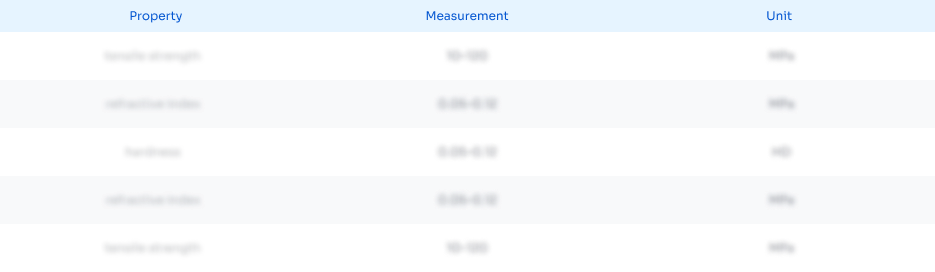
Abstract
Description
Claims
Application Information

- R&D Engineer
- R&D Manager
- IP Professional
- Industry Leading Data Capabilities
- Powerful AI technology
- Patent DNA Extraction
Browse by: Latest US Patents, China's latest patents, Technical Efficacy Thesaurus, Application Domain, Technology Topic, Popular Technical Reports.
© 2024 PatSnap. All rights reserved.Legal|Privacy policy|Modern Slavery Act Transparency Statement|Sitemap|About US| Contact US: help@patsnap.com