Bacteriostatic antistatic multifunctional non-woven fabric
A non-woven, multi-functional technology, applied in textiles and papermaking, fiber treatment, ultrasonic/sonic fiber treatment, etc., can solve the problems of insufficient durability and unsatisfactory anti-static effect, and achieve good absorption conversion and light fastness good, large market value and the effect of social value
- Summary
- Abstract
- Description
- Claims
- Application Information
AI Technical Summary
Problems solved by technology
Method used
Image
Examples
Embodiment 1
[0023] Embodiment 1: 0.5 part (weight part, every part 1KG) gamma-aminopropyltriethoxysilane is dissolved in the ratio of 1: 10 in 5 parts of dehydrated alcohol, under stirring state, the nano-silica Add the powder and nano-silver powder to the ethanol solution of γ-aminopropyltriethoxysilane, treat with ultrasonic waves for 30 minutes, then distill under reduced pressure to remove absolute ethanol, and dry to obtain the modified powder for later use; Pour 200 parts of water into the reaction kettle and heat to 75°C, then, under continuous stirring, add 1 part of sodium lauryl sulfate, 0.5 part of hydroxyethyl cellulose, 0.7 part of penetrant JFC, and sorbitan Put 1 part of ester, 5 parts of cetyltrimethylammonium chloride, and 15 parts of methacrylic acid into the reaction kettle and mix them with water, then add 15 parts of β-cyclodextrin, 0.2 parts of spice (lavender essential oil) , stirring for 30 minutes to obtain an emulsion; pour the modified powder into the reaction k...
Embodiment 2
[0024] Example 2: Dissolve 0.3 parts of γ-aminopropyltriethoxysilane in 3 parts of absolute ethanol at a ratio of 1:5, and add nano-silica powder and nano-silver powder to Put it into the ethanol solution of γ-aminopropyltriethoxysilane, treat it with ultrasonic waves for 30 minutes, then distill it under reduced pressure to remove absolute ethanol, dry it, and obtain the modified powder for later use; pour 180 parts of water into the reaction kettle and heat to 75°C, and then under continuous stirring, add 1 part of sodium lauryl sulfate, 1 part of hydroxyethyl cellulose, 0.5 part of penetrant JFC, 0.5 part of sorbitan ester, cetyl tri Put 2 parts of methyl ammonium chloride and 12 parts of methacrylic acid into the reaction kettle and mix them fully with water, then add 18 parts of β-cyclodextrin and 0.5 parts of spice (vanillin), and stir for 30 minutes to obtain an emulsion; The modified powder is poured into the reactor and stirred for 30 minutes to obtain the finishing a...
Embodiment 3
[0025] Example 3: 0.3 parts of γ-aminopropyltriethoxysilane was dissolved in 3 parts of absolute ethanol at a ratio of 1:5, and the nano-silica powder and the nano-silver powder were added to the mixture under stirring. Put it into the ethanol solution of γ-aminopropyltriethoxysilane, treat it with ultrasonic waves for 30 minutes, then distill it off under reduced pressure to remove absolute ethanol, dry it, and obtain the modified powder for later use; pour 170 parts of water into the reaction kettle Heating to 75°C, and under continuous stirring, add 1.5 parts of sodium lauryl sulfate, 0.7 parts of hydroxyethyl cellulose, 0.6 parts of penetrant JFC, 0.7 parts of sorbitan ester, cetyl 3 parts of trimethylammonium chloride and 13 parts of methacrylic acid were put into the reaction kettle and fully mixed with water, then 13 parts of β-cyclodextrin and 0.3 parts of fragrance (dimethylbenzyl acetate) were added, and stirred for 30 The emulsified product is obtained in 1 minute, ...
PUM
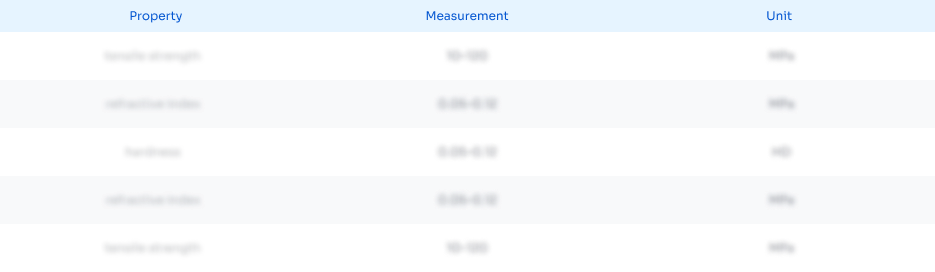
Abstract
Description
Claims
Application Information

- R&D
- Intellectual Property
- Life Sciences
- Materials
- Tech Scout
- Unparalleled Data Quality
- Higher Quality Content
- 60% Fewer Hallucinations
Browse by: Latest US Patents, China's latest patents, Technical Efficacy Thesaurus, Application Domain, Technology Topic, Popular Technical Reports.
© 2025 PatSnap. All rights reserved.Legal|Privacy policy|Modern Slavery Act Transparency Statement|Sitemap|About US| Contact US: help@patsnap.com