Method for preparing catalyst for preparing synthesis gas by reforming methane and carbon dioxide
A carbon dioxide and catalyst technology, which is applied in the field of preparing synthesis gas catalysts by methane-carbon dioxide reforming, can solve the problems of low reaction performance, loss of active components, high cost and the like, and achieves good carbon deposition resistance, good catalytic activity, Highly selective effect
- Summary
- Abstract
- Description
- Claims
- Application Information
AI Technical Summary
Problems solved by technology
Method used
Examples
Embodiment 1
[0020] Dry γ-alumina at 110°C for 4 hours, impregnate it with the mixed aqueous solution of cerous nitrate and lanthanum nitrate at room temperature for 8 hours by equal volume impregnation method, then dry it at 110°C for 4 hours, and then in air atmosphere at 600°C Roast for 4 hours. The modified support was immersed in nickel acetate solution at room temperature for 8 hours, then dried at 110° C. for 4 hours, and then calcined at 600° C. in air for 4 hours. The catalyst precursor (I) was obtained by immersing the impregnated active component nickel sample in chloroplatinic acid solution for 8 hours at room temperature, and then roasting at 600° C. for 4 hours in an air atmosphere. The total mass content of cerium oxide and lanthanum oxide in the catalyst is 1%, wherein the molar ratio of cerium oxide and lanthanum oxide is 1:1, the content of nickel is 10%, and the content of platinum is 0.02%.
[0021] The performance test of the prepared catalyst in the reaction of metha...
Embodiment 2
[0023] Nickel-aluminum spinel (NiAl 2 o 4 ) as a carrier, without Ni salt impregnation process, others are the same as in Example 1, and the prepared catalyst precursor is (II). The test method of catalyst reaction performance is the same as embodiment 1, and the catalyst methane conversion ratio prepared by precursor (II) is 96.2%, and carbon dioxide conversion ratio is 92.3%, and product CO, H 2 The selectivities are respectively: 97.5%, 97.6%.
Embodiment 3
[0025] Dry γ-alumina at 110°C for 4 hours, use the equal volume impregnation method to impregnate the mixed aqueous solution of cerous nitrate, lanthanum nitrate, and nickel nitrate at room temperature for 12 hours, then dry at 110°C for 4 hours, and then in the air atmosphere Calcined at 800°C for 2 hours. The catalyst precursor (III) was obtained by immersing a sample impregnated with nickel as an active component in a chloroplatinic acid solution for 12 hours at room temperature, and then calcining at 800° C. for 4 hours in an air atmosphere. The total mass content of cerium oxide and lanthanum oxide in the catalyst is 1%, wherein the molar ratio of cerium oxide and lanthanum oxide is 1:1, the content of nickel is 10%, and the content of platinum is 1.0%. The test method of the catalyst reaction performance is the same as that of Example 1. The methane conversion rate of the catalyst prepared by the precursor (III) is 96.0%, and the carbon dioxide conversion rate is 92.0%. ...
PUM
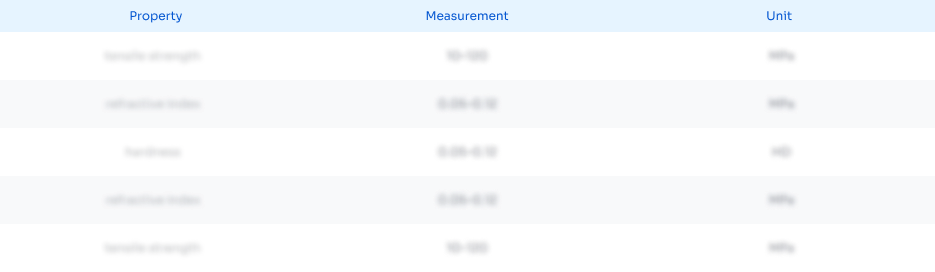
Abstract
Description
Claims
Application Information

- R&D
- Intellectual Property
- Life Sciences
- Materials
- Tech Scout
- Unparalleled Data Quality
- Higher Quality Content
- 60% Fewer Hallucinations
Browse by: Latest US Patents, China's latest patents, Technical Efficacy Thesaurus, Application Domain, Technology Topic, Popular Technical Reports.
© 2025 PatSnap. All rights reserved.Legal|Privacy policy|Modern Slavery Act Transparency Statement|Sitemap|About US| Contact US: help@patsnap.com