Continuous film forming apparatus
A film-forming roller and plasma technology, which is applied in the direction of gaseous chemical plating, coating, electrical components, etc., can solve the problems of film-forming stability damage, sealing effect change, and protective film quality stability decline
- Summary
- Abstract
- Description
- Claims
- Application Information
AI Technical Summary
Problems solved by technology
Method used
Image
Examples
Embodiment Construction
[0021] In the plasma CVD apparatus of the present invention, AC or pulse voltage accompanied by polarity inversion is applied to the film-forming rollers arranged oppositely under reduced pressure. (zone)) to generate a glow discharge, and to form a film by plasma CVD on a tape-shaped base material that is wound up facing the facing space of the film-forming rollers. As the base material, any material can be used as long as it is an insulating material that can be wound in a roll shape, such as a plastic film or sheet, or paper. PET, PEN, PES, polycarbonate, polyolefin, polyimide, etc. are suitable as a plastic film or sheet, and the thickness of the substrate is preferably 5 μm to 0.5 mm that can be transported in a vacuum. In addition, as will be described later, a conductive material can be used as the base material depending on the configuration of the device.
[0022] figure 1 The overall structure of the plasma CVD apparatus according to the embodiment of the present i...
PUM
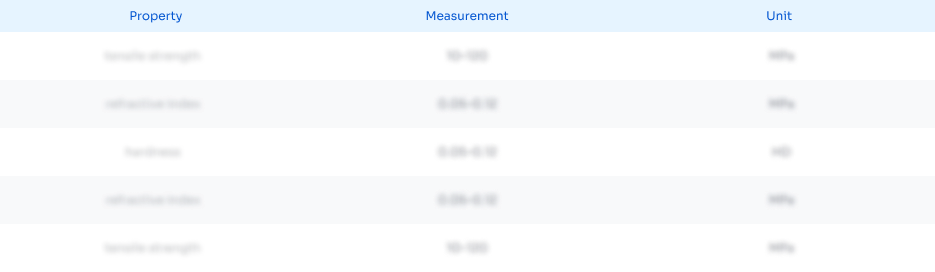
Abstract
Description
Claims
Application Information

- R&D
- Intellectual Property
- Life Sciences
- Materials
- Tech Scout
- Unparalleled Data Quality
- Higher Quality Content
- 60% Fewer Hallucinations
Browse by: Latest US Patents, China's latest patents, Technical Efficacy Thesaurus, Application Domain, Technology Topic, Popular Technical Reports.
© 2025 PatSnap. All rights reserved.Legal|Privacy policy|Modern Slavery Act Transparency Statement|Sitemap|About US| Contact US: help@patsnap.com