Method for manufacturing calcium aluminate cement by adopting alloy slag
A technology for calcium aluminate cement and slag, which is applied in the field of calcium aluminate cement manufacturing, can solve the problems of high manufacturing cost, low added value, and does not meet environmental protection requirements, and achieves the effects of low manufacturing cost and high added value.
- Summary
- Abstract
- Description
- Claims
- Application Information
AI Technical Summary
Problems solved by technology
Method used
Examples
Embodiment 1
[0010] The aluminothermic reduction method smelting ferrovanadium or vanadium-aluminum slag is crushed to 200 mesh by a crusher, and then powdered; add sodium carbonate (sodium chloride or sodium sulfate can also be added) according to 10% of the total weight of the powder, and grind it in a rotary kiln or Roasted at high temperature in a shaft furnace at a furnace temperature of 1000°C or 1200°C for 3 hours; the roasted material was leached in hot water at 60°C for 120 minutes, and then filtered; the filtrate was passed through sulfuric acid (or hydrochloric acid) to adjust the pH value to 1.5, Add ammonium sulfate (or ammonium chloride) according to the weight ratio of vanadium in the filtrate to 1:1, heat to 80°C, precipitate ammonium polyvanadate after 120 minutes, and then melt it into vanadium pentoxide at a high temperature of 850°C. sale; the filter residue is washed, dried, and milled through 240 mesh to produce calcium aluminate cement.
Embodiment 2
[0012] The aluminothermic reduction method smelting ferrovanadium or vanadium-aluminum slag is crushed to 320 mesh by a crusher, and then powdered; add sodium carbonate (sodium chloride or sodium sulfate can also be added) according to 30% of the total weight of the powder, and use it in a rotary kiln or Roast in a shaft furnace at high temperature at 1400°C for 1 hour; the roasted material is leached in hot water at 98°C for 30 minutes, then filtered; add sulfuric acid (or hydrochloric acid) to the filtrate to adjust the pH value to 3.5, and press Ammonium sulfate (or ammonium chloride) is added in the vanadium element weight ratio of 1:1, and ammonium polyvanadate is precipitated after heating to 100°C for 30 minutes, and then melted into vanadium pentoxide at 800°C for sale; the filter residue is cleaned , drying, and milling through 320 mesh to obtain calcium aluminate cement.
Embodiment 3
[0014] The aluminothermic reduction method smelting ferrovanadium or vanadium-aluminum slag is crushed to 300 mesh by a crusher, and then powdered; add sodium carbonate (sodium chloride or sodium sulfate can also be added) according to 20% of the total weight of the powder, and grind it in a rotary kiln or Roasted in a shaft furnace at high temperature at 1280°C for 2.5 hours; the roasted material was leached in hot water at 78°C for 90 minutes and then filtered; adding sulfuric acid (or hydrochloric acid) to the filtrate to adjust the pH to 2.5 Add ammonium sulfate (or ammonium chloride) at a vanadium element weight ratio of 1:1, heat to 90°C, precipitate ammonium polyvanadate after 90 minutes, and then melt it into vanadium pentoxide at a high temperature of 830°C for sale; the filter residue is cleaned , drying, and milling through 300 mesh to obtain calcium aluminate cement.
PUM
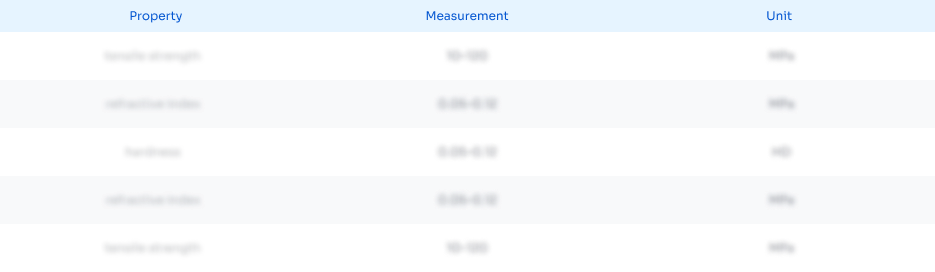
Abstract
Description
Claims
Application Information

- R&D Engineer
- R&D Manager
- IP Professional
- Industry Leading Data Capabilities
- Powerful AI technology
- Patent DNA Extraction
Browse by: Latest US Patents, China's latest patents, Technical Efficacy Thesaurus, Application Domain, Technology Topic, Popular Technical Reports.
© 2024 PatSnap. All rights reserved.Legal|Privacy policy|Modern Slavery Act Transparency Statement|Sitemap|About US| Contact US: help@patsnap.com