Axle bush and sleeve
A technology for bushings and bushings, which is applied in the field of metallurgical industry and hot-coating equipment, can solve the problems of rough wear surface, short service life, and wear-resistant iron-based materials, so as to improve the service life, stability and reliability, and reduce the Thermal expansion coefficient, wear surface smoothing effect
- Summary
- Abstract
- Description
- Claims
- Application Information
AI Technical Summary
Problems solved by technology
Method used
Image
Examples
Embodiment 1
[0033] The components of bearing bush and sleeve are by weight: Si 0.5%, Mn 0.3%, C 0.6%, Al 0.5%, P<0.07%, S<0.07%, V 0.1%, Ti 0.1%, Cr 25%, Fe 6% , Ni 5%, Nb 1.5%, W 3%, Mo 3%, and the rest is Co. The service time of the bearing pad and sleeve in the prior art is obviously lower than that of the bearing pad and sleeve of the present invention in the same unit, and is less than 1 / 3 of the service time of the bearing pad and sleeve of the present invention.
Embodiment 2
[0035] The composition of bearing pad and sleeve is: Al 0.5%, Si 0.4%, Mn 0.7%, C 0.6%, Cr 20%, Fe 12%, Ni 3%, Nb 1.0%, W 5%, Mo 2%, V 0.2%, Ti 0.2%, the rest is Co. The service time of the bearing pad and sleeve in the prior art is obviously lower than that of the bearing pad and sleeve of the present invention in the same unit, and is less than 1 / 3 of the service time of the bearing pad and sleeve of the present invention.
Embodiment 3
[0037] The components of the bushing and sleeve are: Al 0.8%, Si 1.0%, C 1.5%, Mn 0.7%, Cr 26%, Fe 12%, Ni 3%, Nb 1.0%, W 5%, Mo 2%, V 0.2%, Ti 0.2%, the rest is Co. The service time of the bearing pad and sleeve in the prior art is obviously lower than that of the bearing pad and sleeve of the present invention in the same unit, and is less than 1 / 3 of the service time of the bearing pad and sleeve of the present invention.
[0038] Figure 5A A photograph showing the corrosion resistance of a bearing pad bushing according to the invention. Figure 5A It is the appearance of the interface of the cobalt-based alloy according to the present invention after being soaked in the hot-dip galvalume pot for 58 days, wherein, the left side is the cobalt-based alloy, and the right side is the aluminum-zinc liquid. from Figure 5A It can be seen that the tool marks still exist and the interface is clear.
[0039] Figure 5BA photograph showing the corrosion resistance of a bearing ...
PUM
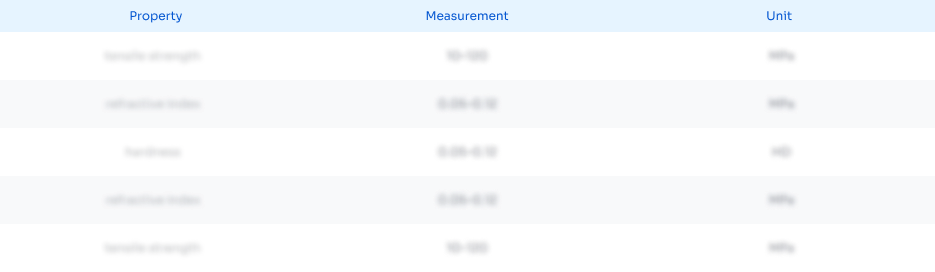
Abstract
Description
Claims
Application Information

- R&D
- Intellectual Property
- Life Sciences
- Materials
- Tech Scout
- Unparalleled Data Quality
- Higher Quality Content
- 60% Fewer Hallucinations
Browse by: Latest US Patents, China's latest patents, Technical Efficacy Thesaurus, Application Domain, Technology Topic, Popular Technical Reports.
© 2025 PatSnap. All rights reserved.Legal|Privacy policy|Modern Slavery Act Transparency Statement|Sitemap|About US| Contact US: help@patsnap.com