Delayed coking process
A delayed coking and process technology, which is applied in the field of delayed coking process, can solve the problems of increased coking tendency, high investment and energy consumption of coking heating furnace tubes
- Summary
- Abstract
- Description
- Claims
- Application Information
AI Technical Summary
Problems solved by technology
Method used
Image
Examples
Embodiment 1
[0039] The 130°C heavy oil I (see Table 1 for its properties) is pumped and mixed with the circulating oil from the coking fractionation tower, and then enters the preheating furnace (that is, the convection chamber and radiation chamber of the heating furnace of the delayed coking industrial device) to be heated. The preheating furnace The water vapor injection rate is 0.82% (accounting for the amount of heavy oil, the same below), and the temperature of the material at the outlet of the preheating furnace is controlled to be 417°C, and then enters the upflow visbreaking reactor for visbreaking, and the material stays in the visbreaking reactor The time is 42 minutes, the temperature at the top of the visbreaking reactor is 408° C., and the gauge pressure is 0.53 MPa (to overcome the resistance of the system).
[0040] The visbroken mixture exiting the visbreaking reactor enters the heating furnace (i.e. the radiation chamber of the heating furnace of the delayed coking indust...
Embodiment 2
[0049] Visbreaking conditions were the same as in Example 1, but the visbreaking feed did not include cycle oil. After cooling, separating and analyzing the visbroken mixture of the visbroken heavy oil I, the product distribution and main properties of the visbroken heavy oil are listed in Table 3.
[0050] Comparing Table 1 and Table 3, the viscosities of the visbreaking heavy oil at 80°C and 100°C are 51.98% and 47.64% of the raw oil, and the visbreaking effect is obvious.
[0051] Table 3 Product distribution of visbroken heavy oil I and main properties of visbroken heavy oil
[0052]
Embodiment 3
[0054] Investigation on coking tendency of heavy oil and its visbroken in heating furnace tube.
PUM
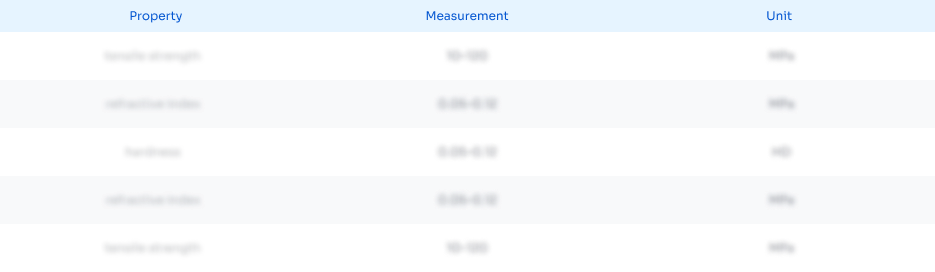
Abstract
Description
Claims
Application Information

- R&D
- Intellectual Property
- Life Sciences
- Materials
- Tech Scout
- Unparalleled Data Quality
- Higher Quality Content
- 60% Fewer Hallucinations
Browse by: Latest US Patents, China's latest patents, Technical Efficacy Thesaurus, Application Domain, Technology Topic, Popular Technical Reports.
© 2025 PatSnap. All rights reserved.Legal|Privacy policy|Modern Slavery Act Transparency Statement|Sitemap|About US| Contact US: help@patsnap.com