Method for actively packaging blue light LED chip based white light LED
A technology of LED chips and packaging methods, which is applied in the direction of electrical components, circuits, semiconductor devices, etc., can solve the problems of multiple processes, low production efficiency, and high cost, and achieve the effects of high process repeatability, high packaging efficiency, and short production time
- Summary
- Abstract
- Description
- Claims
- Application Information
AI Technical Summary
Problems solved by technology
Method used
Image
Examples
Embodiment
[0049] Example product test report
[0050] An advantage of the method of the present invention for packaging white light LEDs is that the light emitted by the LED chip itself is used to trigger the curing of the photosensitive resin, and the fluorescent powder is distributed in the resin lens as required, which can effectively solve the disadvantages of uneven fluorescent powder. After the sample is packaged, its light emission angle is greatly increased, close to 165°, while the prior art method of adding hemispherical lens molding and packaging can only reach 120°, its spatial distribution is more even, and the light emission effect is better. The test results of light and color parameters (without heat sink) show that the light radiation power, luminous flux, and luminous efficacy of this sample have met the commercial requirements of similar products, of which the luminous flux is 41.81m, and the luminous efficacy is 41.21m / W. The color rendering is higher than that of ge...
PUM
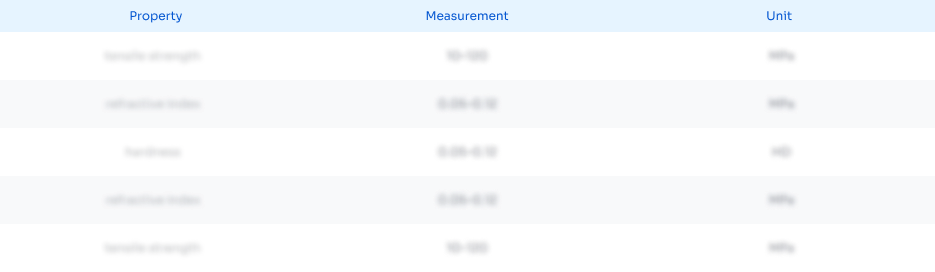
Abstract
Description
Claims
Application Information

- Generate Ideas
- Intellectual Property
- Life Sciences
- Materials
- Tech Scout
- Unparalleled Data Quality
- Higher Quality Content
- 60% Fewer Hallucinations
Browse by: Latest US Patents, China's latest patents, Technical Efficacy Thesaurus, Application Domain, Technology Topic, Popular Technical Reports.
© 2025 PatSnap. All rights reserved.Legal|Privacy policy|Modern Slavery Act Transparency Statement|Sitemap|About US| Contact US: help@patsnap.com