Method for catalyzing and transforming naphtha
A naphtha and catalyst technology, applied in the field of catalytic conversion of naphtha, can solve the problem of less research on expanding the source of reforming raw materials, and achieve the effect of broadening the source of raw materials
- Summary
- Abstract
- Description
- Claims
- Application Information
AI Technical Summary
Problems solved by technology
Method used
Image
Examples
preparation example Construction
[0043]The preparation method adopted for the above-mentioned hydroaromatization catalyst is as follows: after mixing the zeolite and the binder, use the acetic acid aqueous solution as the peptizer, knead and extrude into a strip, dry and roast at 500-650°C for 4-6 hours to obtain Carrier, load Group VIII metals, alkali metals or alkaline earth metals and halogens on the formed carrier at the same time by co-impregnation method, dry at 50-120°C for 4-12 hours, bake at 200-350°C for 4-6 hours, 300-500 ℃ hydrogen reduction for 1 to 6 hours.
[0044] The non-hydroaromatization catalyst comprises 0.5-5.0 mass % of metal oxides selected from zinc, molybdenum or gallium, 0.1-5.0 mass % of rare earth oxides, 1.0-7.0 mass % of VA group elements and 83.0 ~98.4% by mass of composite carrier, the composite carrier includes 20-70% by mass of ZSM series zeolite or MCM series zeolite and 30-80% by mass of binder. The VA group element is preferably phosphorus, antimony or bismuth, more pref...
example 1
[0065] This example prepares hydrorefined naphtha.
[0066] Hydrocracked oil with ASTM D-86 boiling range of 95-258°C, coker oil with 50-166°C, catalytic cracked oil with 42-163°C, normal pressure priming oil with 58-89°C and 91-182°C Straight-run naphtha is made into mixed raw material oil according to the mass ratio of 50:20:5:5:20.
[0067] The above-mentioned mixed feedstock oil was heated at 290°C, the hydrogen partial pressure was 2.0 MPa, the hydrogen / hydrocarbon volume ratio was 200:1, and the feed volume space velocity was 8.0 hours -1 Hydrofining is carried out in the presence of hydrogenation catalyst A under certain conditions. The reaction product is sent to a water cooler, separated into two phases of gas and liquid, measured separately and analyzed for composition. The hydrogenation catalyst A contains 0.03% by mass of CoO, 2.0% by mass of NiO, and 19.0% by mass of WO 3 and 78.97% by mass of Al 2 o 3 . The properties of raw oil before and after hydrofining...
example 2
[0069] Preparation of catalysts for the lightening reaction of heavy fractions.
[0070] (1) Preparation of Beta molecular sieves with low aluminum content and boron.
[0071] 0.5g pseudo-boehmite powder (Germany Condea company, trade mark SB), 2.0g borax, 2.2gNaOH and 209.4g concentration are 25 mass % tetraethylammonium hydroxide solution and mix uniformly, then add 40g ultrafine silicon dioxide (manufactured by Cabot Company, brand name CAB-O-SILM-5), stirred evenly, moved into the reaction kettle, crystallized at 140°C for 10 days, and cooled rapidly to 40°C after the crystallization was completed. After the product was centrifuged and washed, the resulting solid was 120 °C and dried for 10 hours to obtain the original powder a of Beta molecular sieve with low aluminum content and boron.
[0072] (2) Preparation of Beta / ZSM-5 composite borosilicate molecular sieve with low aluminum content.
[0073] Mix 3.7g of borax, 0.4g of NaOH, 4.88g of tetraethylammonium hydroxide s...
PUM
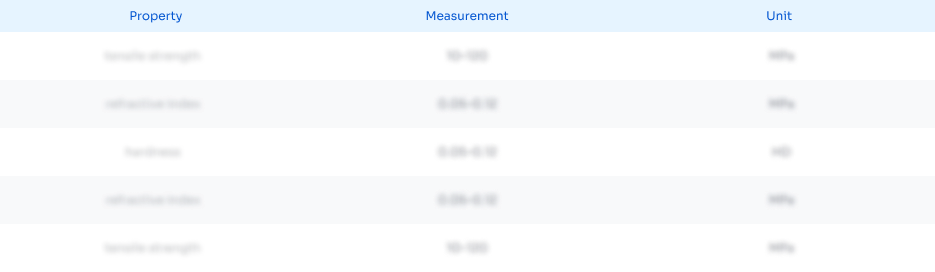
Abstract
Description
Claims
Application Information

- Generate Ideas
- Intellectual Property
- Life Sciences
- Materials
- Tech Scout
- Unparalleled Data Quality
- Higher Quality Content
- 60% Fewer Hallucinations
Browse by: Latest US Patents, China's latest patents, Technical Efficacy Thesaurus, Application Domain, Technology Topic, Popular Technical Reports.
© 2025 PatSnap. All rights reserved.Legal|Privacy policy|Modern Slavery Act Transparency Statement|Sitemap|About US| Contact US: help@patsnap.com