Vertical stripping processing technology for manufacturing seamless thin wall pipe
A thin-walled tube and vertical technology, applied in metal rolling and other directions, can solve problems such as easy eccentricity, affecting printing quality of printing equipment, uniformity of wall thickness, poor cylindricality and smoothness, etc.
- Summary
- Abstract
- Description
- Claims
- Application Information
AI Technical Summary
Problems solved by technology
Method used
Image
Examples
Embodiment Construction
[0017] now attached image 3 Elaborate the present invention in detail:
[0018] The vertical rolling process for producing seamless thin-walled tubes, the process steps are as follows:
[0019] a. Install the mold core column vertically on the machine tool, the machine tool can control the mold core column to make clockwise or counterclockwise self-propagation movement, and control the mold core column to move back and forth in the axial direction;
[0020] b. Lay a thin-walled plate with a wall thickness of 0.5mm on the top of the core column, and adjust the spraying position of the cooling liquid;
[0021] c. Set three rolling rollers evenly near the top circumference of the thin-walled plate, and adjust the gap between the rolling rollers and the mold core core column to the wall thickness of the required thin-walled pipe;
[0022] d. Start the rolling roller, make the rolling roller do the self-propagation movement, and at the same time make a vertical relative movement...
PUM
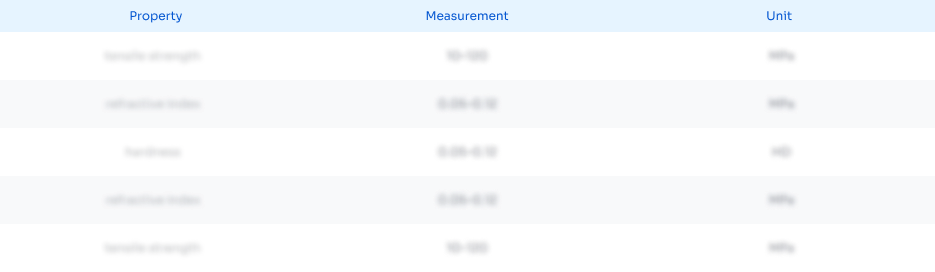
Abstract
Description
Claims
Application Information

- Generate Ideas
- Intellectual Property
- Life Sciences
- Materials
- Tech Scout
- Unparalleled Data Quality
- Higher Quality Content
- 60% Fewer Hallucinations
Browse by: Latest US Patents, China's latest patents, Technical Efficacy Thesaurus, Application Domain, Technology Topic, Popular Technical Reports.
© 2025 PatSnap. All rights reserved.Legal|Privacy policy|Modern Slavery Act Transparency Statement|Sitemap|About US| Contact US: help@patsnap.com