Low Temperature Ammonia Selective Catalytic Oxidation Catalyst
A catalyst and selectivity technology, applied in physical/chemical process catalysts, metal/metal oxide/metal hydroxide catalysts, inorganic chemistry, etc., can solve the problems of poor selectivity, low temperature window, high preparation cost, etc. Achieve the effects of simple preparation process, convenient operation and simple preparation method
- Summary
- Abstract
- Description
- Claims
- Application Information
AI Technical Summary
Problems solved by technology
Method used
Image
Examples
Embodiment 1
[0014] Take 100 grams of gamma-alumina powder carrier (specific surface area: 250 square meters per gram), and slowly pour it into 500 milliliters of an aqueous solution in which 15.75 grams of silver nitrate and 30.97 grams of cerium nitrate are dissolved under continuous stirring. After stirring for 1 hour, the water was evaporated to dryness with a rotary evaporator, and dried overnight at 120°C. The dried catalyst was heated from room temperature to 600° C. at a rate of 10° C. per minute in an air atmosphere, and calcined at 600° C. for 3 hours. The 20-40 mesh particles were sieved for later use, that is, the catalyst of Example 1 was prepared. The prepared chemical composition is 10%Ag / 10%Ce / Al 2 o 3 oxidation catalyst.
Embodiment 2
[0016] Take 100 grams of gamma-alumina powder carrier (specific surface area: 250 square meters per gram), and slowly pour it into 500 milliliters of an aqueous solution in which 15.75 grams of silver nitrate is dissolved under continuous stirring. After stirring for 1 hour, the water was evaporated to dryness with a rotary evaporator, and dried overnight at 120°C. The dried catalyst was heated from room temperature to 600° C. at a rate of 10° C. per minute in an air atmosphere, and calcined at 600° C. for 3 hours. The granules of 20-40 mesh were sieved for later use, that is, the catalyst of Example 2 was prepared. The prepared chemical composition is 10%Ag / Al 2 o 3 oxidation catalyst.
Embodiment 3
[0018] Weigh 0.2 g of the catalyst of Example 1 and place it in a tubular fixed-bed reactor for reaction.
[0019] The reaction gas is simulated industrial ammonia pollution waste gas. Gas composition: the total flow rate of mixed gas is 200 ml per minute, of which, oxygen is 10%, ammonia is 500 ppm, and nitrogen is the balance gas. The reaction space velocity (GHSV) was 20,000 / hour for the catalyst. The reaction temperature range is from room temperature to 220°C. Ammonia and product concentrations were determined using an infrared gas cell.
[0020] The reaction results show that the conversion rate of ammonia exceeds 80% at 100°C; the conversion rate of ammonia is close to 100% at 120°C; and the conversion rate of ammonia reaches 100% at temperatures above 160°C.
[0021] Table 1 10%Ag / 10%Ce / Al 2 o 3 Catalyst Activity Evaluation Results
[0022]
PUM
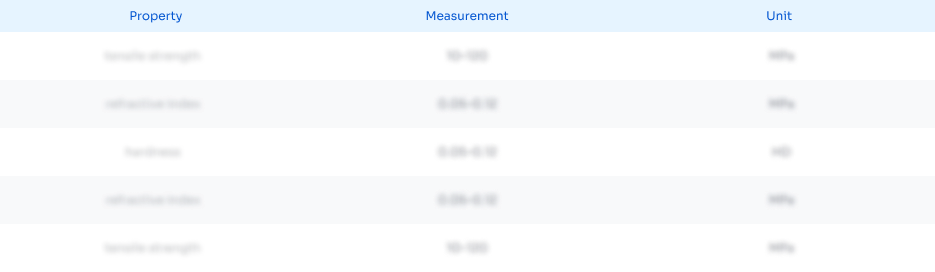
Abstract
Description
Claims
Application Information

- R&D Engineer
- R&D Manager
- IP Professional
- Industry Leading Data Capabilities
- Powerful AI technology
- Patent DNA Extraction
Browse by: Latest US Patents, China's latest patents, Technical Efficacy Thesaurus, Application Domain, Technology Topic, Popular Technical Reports.
© 2024 PatSnap. All rights reserved.Legal|Privacy policy|Modern Slavery Act Transparency Statement|Sitemap|About US| Contact US: help@patsnap.com