Poly-generation technique for using coal gas and coke oven gas as raw materials
A coke oven gas and coal-to-gas technology, applied in the direction of gas fuel, combustible gas production, sustainable manufacturing/processing, etc., can solve the problems of waste of coal resources, emission loss, etc., to save investment, maximize the economy, and improve the economy sexual effect
- Summary
- Abstract
- Description
- Claims
- Application Information
AI Technical Summary
Problems solved by technology
Method used
Image
Examples
Embodiment 1
[0035] In the process of coal gasification, the coal is pre-treated and sprayed into the ash fusion gasification furnace at a temperature of 1000 ° C and a pressure of 1.0 MPa to chemically react with water vapor and pure oxygen from air separation to generate CO, H 2 , CO 2 、H 2 O and a small amount of CH 4 、H 2 Water gas with S, COS and other components. The water gas containing a small amount of dust and impurities is initially purified. Due to the dusty water gas from gasification, it still contains acid gas after being washed, dedusted and cooled by Venturi scrubber and carbon scrubber. In order to protect the compressor, the desulfurization method is also used. Make H 2 S content is less than 30mg / Nm 3 , the preliminary purified water gas is compressed to a pressure of 2.5MPa, and then deeply purified. Deep purification adopts polyethylene glycol dimethyl ether (NHD) method for desulfurization and decarburization. Removed H 2 S gas desulfurization recovery unit...
Embodiment 2
[0037] In the coal gasification process, the coal is pre-treated to make 65% coal water slurry and sprayed into the Texaco gasifier at a temperature of 1300 ° C and a pressure of 7.0 MPa to obtain pure oxygen with gasified water vapor and air separation. Carry out a chemical reaction to produce CO, H 2 , CO 2 、H 2 O and a small amount of CH 4 、H 2 Water gas with S, COS and other components. The gasified dusty water gas, after being washed, dedusted and cooled by Venturi scrubber and carbon washing tower, enters deep purification, in which low-temperature methanol washing process is used for desulfurization and decarbonization. Removed H 2 S gas desulfurization recovery unit recovers sulfur and removes CO 2 To urea synthesis. The deeply purified water gas, coke oven gas pressure swing adsorption hydrogen compressed to 2.0MPa pressure and the tail gas recycled after Fischer-Tropsch synthesis are mixed into fresh Fischer-Tropsch synthesis gas, H 2 S content is less than 0...
Embodiment 3
[0039] In the coal gasification process, the coal is pre-treated to make 65% coal-water slurry and sprayed into the Texaco gasifier at a temperature of 1450 ° C and a pressure of 6.0 MPa to form pure oxygen with gasified water vapor and air separation. Carry out a chemical reaction to produce CO, H 2 , CO 2 、H 2 O and a small amount of CH 4 、H 2 Water gas with S, COS and other components. The gasified dusty water gas, after being washed, dedusted and cooled by Venturi scrubber and carbon washing tower, enters deep purification, in which low-temperature methanol washing process is used for desulfurization and decarbonization. Removed H 2 S gas desulfurization recovery unit recovers sulfur and removes CO 2 To urea synthesis. The deeply purified water gas, coke oven gas pressure swing adsorption hydrogen compressed to 5.0MPa and the tail gas recycled after Fischer-Tropsch synthesis are mixed to form fresh Fischer-Tropsch synthesis gas, H 2 S content is less than 0.1ppm, h...
PUM
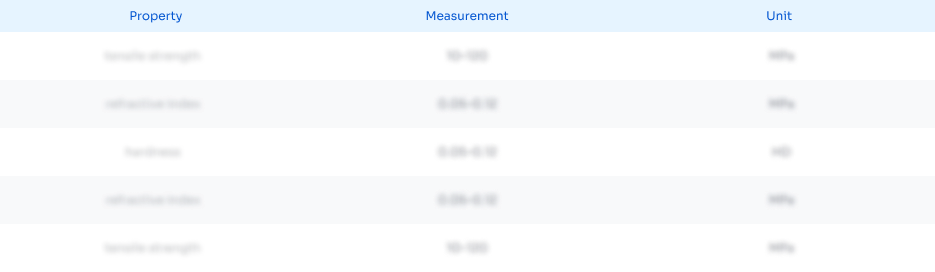
Abstract
Description
Claims
Application Information

- R&D Engineer
- R&D Manager
- IP Professional
- Industry Leading Data Capabilities
- Powerful AI technology
- Patent DNA Extraction
Browse by: Latest US Patents, China's latest patents, Technical Efficacy Thesaurus, Application Domain, Technology Topic, Popular Technical Reports.
© 2024 PatSnap. All rights reserved.Legal|Privacy policy|Modern Slavery Act Transparency Statement|Sitemap|About US| Contact US: help@patsnap.com