Totally closed production technology of paints
A production process, fully enclosed technology, applied in coatings, chemical industry, sustainable manufacturing/processing, etc., can solve the problems of unsolved control technology, many equipment pumps, and difficulty, and achieve the effect of improving the working environment
- Summary
- Abstract
- Description
- Claims
- Application Information
AI Technical Summary
Problems solved by technology
Method used
Image
Examples
Embodiment 1
[0024] Embodiment one, three-layer three-dimensional production process makes solvent-based antirust primer
[0025] 1. Check and ensure that all valves and switches are closed before production, and accurately weigh the following materials according to the formula:
[0026] 200 parts of alkyd resin, 140 parts of zinc chrome yellow, 15 parts of mixed dry material
[0027] Phenolic paint 60+100 parts Zinc oxide 120 parts
[0028] Bentonite 5 parts Talcum powder 50 parts
[0029] CP-88 anti-settling agent 3 parts Precipitated barium sulfate 165 parts
[0030] 200# gasoline 140 parts anti-skinning agent 2 parts
[0031]2. Open the exhaust gas collection valve C, and then open the feed valve A, inject 200 parts of alkyd resin and 60 parts of phenolic paint from the resin storage tank into the mixing pot 1 by using an ultrasonic metering pump, and open the feed valve B to feed the 140 parts of 200# gasoline in the solvent storage tank are also poured into the mixing pot 1, and ...
Embodiment 2
[0035] Embodiment two, three-layer three-dimensional production process makes solvent-type white alkyd topcoat
[0036] 1. Check and ensure that all valves and switches are closed before production, and accurately weigh the following materials according to the formula:
[0037] Alkyd resin 300+240 parts Titanium dioxide 140 parts
[0038] 76 parts of 200# gasoline Ultramarine 1 part
[0039] 5 parts of bentonite, 210 parts of precipitated barium sulfate
[0040] CP-88 anti-sedimentation agent 3 parts cobalt liquid 1 part
[0041] 1 part of lead liquid, 3 parts of anti-skinning agent
[0042] 2. Open the exhaust gas collection valve C, and then open the feed valve A, inject 300 parts of alkyd resin from the resin storage tank into the mixing pot 1 with an ultrasonic metering pump, open the feed valve B to feed 76 parts of alkyd resin from the solvent storage tank 200# gasoline is also poured into the mixing pot 1, and continue to add 5 parts of bentonite, 3 parts of CP-88 a...
Embodiment 3
[0046] Embodiment three, two-layer three-dimensional production method make water-based acrylic baking varnish
[0047] 1. Check and ensure that all valves and switches are closed before production, and accurately weigh the following materials according to the formula:
[0048] Water-based acrylic resin 440+100 parts Propylene glycol methyl ether 50+30 parts
[0049] Bentonite 2 parts Defoamer 2+1 parts
[0050] Wetting and dispersing agent 3 parts High wear-resistant carbon black 40 parts
[0051] 50 parts of butanol 130 parts of purified water
[0052] Precipitated barium sulfate 100 parts
[0053] 2. Open the exhaust gas collection valve C, and then open the feed valve A, inject 440 parts of water-based acrylic resin from the resin storage tank into the mixing pot with an ultrasonic metering pump, open the feed valve B to feed 50 parts of Ding from the solvent storage tank Alcohol, 50 parts of propylene glycol methyl ether, and 130 parts of pure water are also poured in...
PUM
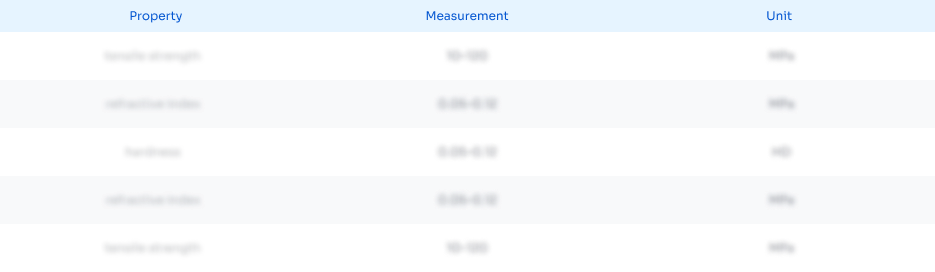
Abstract
Description
Claims
Application Information

- R&D Engineer
- R&D Manager
- IP Professional
- Industry Leading Data Capabilities
- Powerful AI technology
- Patent DNA Extraction
Browse by: Latest US Patents, China's latest patents, Technical Efficacy Thesaurus, Application Domain, Technology Topic, Popular Technical Reports.
© 2024 PatSnap. All rights reserved.Legal|Privacy policy|Modern Slavery Act Transparency Statement|Sitemap|About US| Contact US: help@patsnap.com