Pin tool for friction stir welding and ultrafine grain preparation method thereof
A friction stir welding and friction stir technology, used in welding equipment, non-electric welding equipment, manufacturing tools, etc., can solve the problems of difficult welding of high melting point metals, harsh process conditions, high preparation costs, etc., to reduce welding costs and strengthen joints. The effect of performance and low cost of use
- Summary
- Abstract
- Description
- Claims
- Application Information
AI Technical Summary
Problems solved by technology
Method used
Image
Examples
example 1
[0073] Example 1: Using this method and equipment to process pure copper materials, the process parameters are as follows: stirring head rotation speed 300-1500rmp, electromagnetic vibration frequency 120-250Hz, electromagnetic vibration amplitude 1-2mm, stirring speed 0.1-1.2m / min , liquid nitrogen 10-30L / min.
example 2
[0074]Example 2: Using this method of electromagnetic vibration combined with electromagnetic action friction stir welding of 1.6mm thick 304L stainless steel, the process parameters are as follows: stirring head rotation speed 800-2000rmp, electromagnetic vibration frequency 180-250Hz, electromagnetic vibration amplitude 0.2-1mm, The welding speed is 0.1-1.2m / min, and the flow rate of cold nitrogen protection is 20-50L / min.
[0075] The reasonable matching of electromagnetic vibration process parameters, electromagnetic field process parameters and friction stir welding process parameters should be considered comprehensively, so that electromagnetic vibration, electromagnetic field, shielding gas, weld temperature control and other means can be organically combined, and the main The process parameters are systematically optimized, which guarantees high-quality welded joints or high-quality functional layers.
PUM
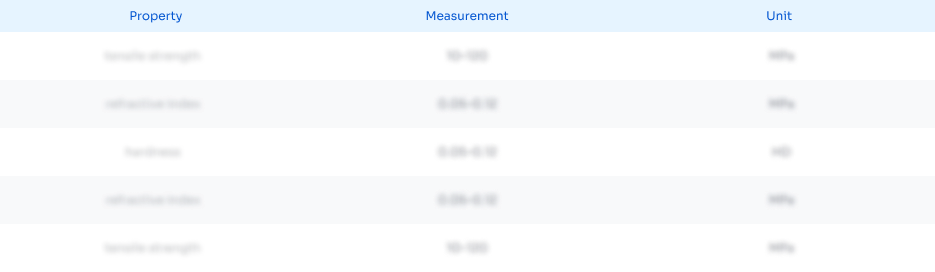
Abstract
Description
Claims
Application Information

- Generate Ideas
- Intellectual Property
- Life Sciences
- Materials
- Tech Scout
- Unparalleled Data Quality
- Higher Quality Content
- 60% Fewer Hallucinations
Browse by: Latest US Patents, China's latest patents, Technical Efficacy Thesaurus, Application Domain, Technology Topic, Popular Technical Reports.
© 2025 PatSnap. All rights reserved.Legal|Privacy policy|Modern Slavery Act Transparency Statement|Sitemap|About US| Contact US: help@patsnap.com