Closed type calcium carbide furnace charging nozzle and process for producing same
A calcium carbide furnace, a closed technology, applied in the direction of manufacturing tools, metal processing equipment, furnaces, etc., can solve the problems of negative impact on production cost and output quality, influence of furnace conditions on calcium carbide quality, and easy burnout of feed nozzles, etc., to achieve improvement Material layer quality structure, process operation control, high yield, high quality, low energy consumption, and reduced heat loss
- Summary
- Abstract
- Description
- Claims
- Application Information
AI Technical Summary
Problems solved by technology
Method used
Image
Examples
Embodiment
[0015] As shown in the figure, the charging nozzle of the enclosed calcium carbide furnace of the present invention consists of two sets of seamless outer sleeve 8, seamless inner sleeve 9, water inlet pipe 3, water outlet pipe 4, connecting pipe 5, and bottom flange 7 The seamless inner sleeve 9 is placed in the seamless outer sleeve 8, the bottom is inlaid with a flange 7, the water inlet pipe 3 and the water outlet pipe 4 are respectively installed on two sets of seamless outer pipes, and the connecting pipe 5 connects the two Set of seamless jacket tubes. Install the hanging plate 1 and the hanging ears 2 on the two sets of seamless outer pipes, with a reinforced triangular plate 6 at the bottom.
[0016] Production Method:
[0017] After the outer sleeve 8 and the inner sleeve 9 are sleeved, the outer sleeve 8 and the inner sleeve 9 are separated by a bottom flange 7 and spot welded in sections. After the spot welding is firm, use the same method to make it. The other one, a...
PUM
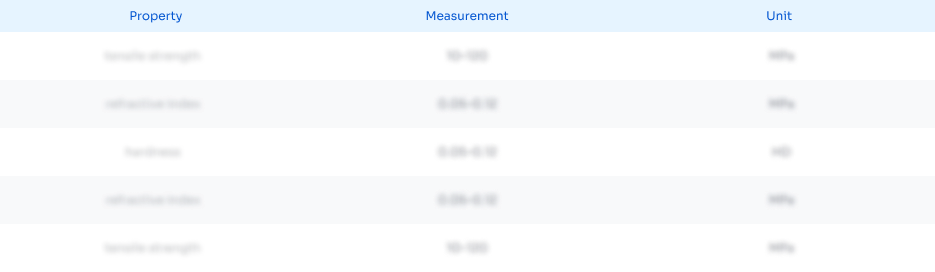
Abstract
Description
Claims
Application Information

- R&D
- Intellectual Property
- Life Sciences
- Materials
- Tech Scout
- Unparalleled Data Quality
- Higher Quality Content
- 60% Fewer Hallucinations
Browse by: Latest US Patents, China's latest patents, Technical Efficacy Thesaurus, Application Domain, Technology Topic, Popular Technical Reports.
© 2025 PatSnap. All rights reserved.Legal|Privacy policy|Modern Slavery Act Transparency Statement|Sitemap|About US| Contact US: help@patsnap.com