Super-thick T2-316L explosion welding superconducting corrosion-resisting composite board
An explosive welding and high corrosion resistance technology, applied in welding equipment, explosives, non-electric welding equipment, etc., can solve the problems of high temperature of explosives, excessive melting of double plate edges, low welding compounding rate, etc.
- Summary
- Abstract
- Description
- Claims
- Application Information
AI Technical Summary
Problems solved by technology
Method used
Examples
Embodiment Construction
[0014] Explosive welding of super-thick T2-316L superconducting high-corrosion-resistant composite board.
[0015] 1. Material specifications and performance of base composite board. T2 is a composite board, which has extremely strong electrical and thermal conductivity, with a thickness of 20mm, a length of 3120mm, and a width of 1600mm. The base plate is made of austenitic stainless steel 316L with a thickness of 80mm, a length of 3000mm, and a width of 1500mm
[0016] 2. Explosive formula for explosive welding. The invention adopts emulsion explosive as the main raw material, and adds 12% salt, 17% perlite, 9% saw powder and other substances, and its explosive detonation speed is about 1050m / s.
[0017] 3. Determination of the thickness and gap of the charge. The gap between the composite board and the base plate is 15mm, and the charge thickness is about 11cm.
[0018] 4. Determining the size of base plate and compound plate and medicine box. The composite board is 7 cm longer...
PUM
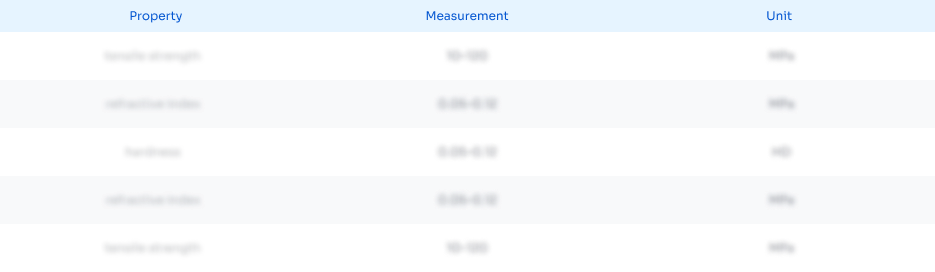
Abstract
Description
Claims
Application Information

- R&D
- Intellectual Property
- Life Sciences
- Materials
- Tech Scout
- Unparalleled Data Quality
- Higher Quality Content
- 60% Fewer Hallucinations
Browse by: Latest US Patents, China's latest patents, Technical Efficacy Thesaurus, Application Domain, Technology Topic, Popular Technical Reports.
© 2025 PatSnap. All rights reserved.Legal|Privacy policy|Modern Slavery Act Transparency Statement|Sitemap|About US| Contact US: help@patsnap.com