Process for producing solvent of red 135
A technology of solvent red and polar organic solvents, which is applied in chemical instruments and methods, organic dyes, organic chemistry, etc., can solve the problems of incomplete recycling, low production cost, and large amount of solvent usage, so as to avoid the relative brightness of products Low, promote the improvement of product grade, and the effect of high product brightness
- Summary
- Abstract
- Description
- Claims
- Application Information
AI Technical Summary
Problems solved by technology
Method used
Image
Examples
Embodiment 1
[0017] In a three-necked flask with stirring and reflux condenser, add 300g 13% hydrochloric acid solution, 60g alcohol, 28.6g tetrachlorophthalic anhydride, 15.8g 1,8-naphthalenediamine, 0.3g fatty alcohol polyoxyethylene ether, turn on the stirring and Heating, heating to reflux, reacting for 10 hours and then filtering, the filter cake is washed with water until the filtrate is neutral, and the product is dried to obtain 40.0 g (98% of the theoretical yield). Compared with the standard product, the product is similar in hue, slightly brighter, similar in depth (see Table 1 for details), and its strength is 101.2%.
[0018] Table 1
[0019] light source △E * △H * △C * △L * △a * △b * D65 / 10 0.86 0.27 0.81 0.15 0.64 0.56 A / 10 0.91 0.31 0.82 0.24 0.50 0.72 F2 / 10 0.94 0.24 0.89 0.20 0.65 0.66
[0020] (Among them: △E—color difference, △H—color difference, △L—lightness difference, △C—chromaticity difference,
[0021] △a—redness-g...
Embodiment 2
[0023] Add 2000kg of 10% hydrochloric acid solution, 150kg of acetic acid, 228kg of tetrachlorophthalic anhydride, 125kg of 1,8-naphthalenediamine, 2kg of nonylphenol polyoxyethylene ether into a 3000L enamel reactor with frame stirring and reflux condenser in sequence, and turn on Stir and heat, heat up to reflux, react for 15 hours and filter, wash the filter cake with clear water until the filtrate is neutral, and dry to obtain 317 kg of product (98.1% of the theoretical yield). Compared with the standard product, the color of the product is similar (see Table 2 for details), and the intensity is 99.1%.
[0024] Table 2
[0025] light source △E * △H * △C * △L * △a * △b * D65 / 10 0.25 0.00 0.21 0.15 0.19 0.08 A / 10 0.39 -0.05 0.34 0.19 0.31 0.15 F2 / 10 0.10 0.01 0.02 0.10 0.01 0.01
Embodiment 3
[0027] Add 3000kg of 13% hydrochloric acid solution, 200kg of dimethylformamide (DMF), 286kg of tetrachlorophthalic anhydride, 158kg of 1,8-naphthalene diamine, 2.5kg of fat in a 5000L enamel reactor with frame stirring and reflux condenser. The alcohol polyoxyethylene ether was stirred and heated, heated to reflux, and filtered after 12 hours of reaction. The filter cake was washed with clean water until the filtrate was neutral and dried to obtain 403 kg of product (98.8% of the theoretical yield). The hue of the product is similar to that of the standard product (see Table 3 for details), and the strength is 100.2%.
[0028] table 3
[0029] light source △E * △H * △C * △L * △a * △b * D65 / 10 0.34 0.07 0.26 0.21 0.21 0.16 A / 10 0.37 0.08 0.27 0.24 0.18 0.22 F2 / 10 0.35 0.07 0.26 0.23 0.19 0.19
PUM
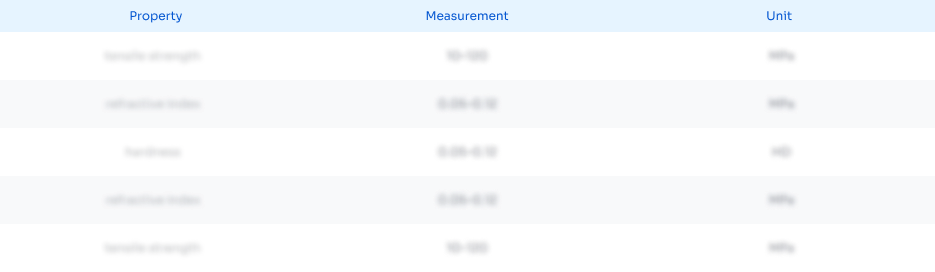
Abstract
Description
Claims
Application Information

- R&D
- Intellectual Property
- Life Sciences
- Materials
- Tech Scout
- Unparalleled Data Quality
- Higher Quality Content
- 60% Fewer Hallucinations
Browse by: Latest US Patents, China's latest patents, Technical Efficacy Thesaurus, Application Domain, Technology Topic, Popular Technical Reports.
© 2025 PatSnap. All rights reserved.Legal|Privacy policy|Modern Slavery Act Transparency Statement|Sitemap|About US| Contact US: help@patsnap.com