Process for indirectly producing ethanol from dimethyl ether
A technology of dimethyl ether and ethanol, applied in the field of ethanol preparation, can solve the problem of high energy consumption, and achieve the effects of reducing three waste discharges, reducing energy consumption, and reducing energy consumption
- Summary
- Abstract
- Description
- Claims
- Application Information
AI Technical Summary
Problems solved by technology
Method used
Image
Examples
Embodiment 1
[0032] The process of preparing methyl acetate by carbonylation of dimethyl ether is as follows: figure 1 shown.
[0033] The carbonylation reactor adopts a tubular fixed-bed reactor, which is filled with a modified hydrogen-type zeolite molecular sieve catalyst. The molar ratio of CO to dimethyl ether was 6.0. The reaction temperature is 210°C and the pressure is 5.6Mpa.
[0034] Carbon monoxide raw material gas 1, temperature 30°C, pressure 5.6MPa, forms a mixed gas with recycle gas 17, temperature 60°C, pressure 5.6MPa After being preheated by preheater E1, stream 2 is formed and enters from the top of vaporizer F1. Dimethyl ether raw material liquid 3, temperature 45°C, pressure 5.6MPa and recycled material 18, temperature 46°C, pressure 5.6MPa are preheated by preheater E2 to form stream 4, which enters from the top of vaporizer F1, Fully mix and vaporize in the vaporizer to form a mixed reaction gas 6, and then heat it through the heater E3 to the temperature required...
Embodiment 2
[0037] This embodiment is a comparative example of embodiment 1, further rectification is carried out to the production liquid 19 of the crude fractionation tower tank, and refined methyl acetate is obtained, and its technological process diagram is as follows figure 2 As shown, the specific implementation is as follows:
[0038]The production fluid 19 of the crude fractionation tower kettle has a temperature of 185 ° C and a pressure of 2.0 MPa. The composition and mass fraction of the product are: methyl acetate: 94.84%, acetic acid 5.14%, enter the refining tower, and the operating pressure of the refining tower is 0.2 MPa. The temperature is 78°C, the temperature of the tower kettle is 128°C, and the reflux ratio is 2. After the tower top steam is condensed by the tower top condenser, part of it is refluxed, and part of it is recovered as refined methyl ester, and the content of methyl acetate is 99.9%. The production liquid in the tower kettle is mainly acetic acid, whi...
Embodiment 3
[0040] This embodiment is to carry out the catalytic hydrogenation of methyl acetate to produce ethanol with the product obtained in embodiment 1 or embodiment 2, and the process flow diagram is as follows image 3 shown. The specific implementation is as follows:
[0041] The hydrogenation reactor is loaded with a modified Cu-based catalyst, and the upper and lower parts are filled with stainless steel magnetic rings with comparable particle sizes, and the mixed solution of methyl acetate and acetic acid (Example 1) or refined methyl acetate (Example 2) is used as the filling. For the liquid raw material, a certain amount of hydrogen is introduced, the molar ratio of hydrogen to ester in the reaction gas is controlled to be 30, the reaction temperature is 205°C, and the pressure is 6.0Mpa.
[0042] Hydrogen raw material gas 20, temperature 40°C, pressure 6.0MPa and return gas 32 composed of circulating gas, temperature 60°C, pressure 6.0MPa, after the heat exchange gas E4 is...
PUM
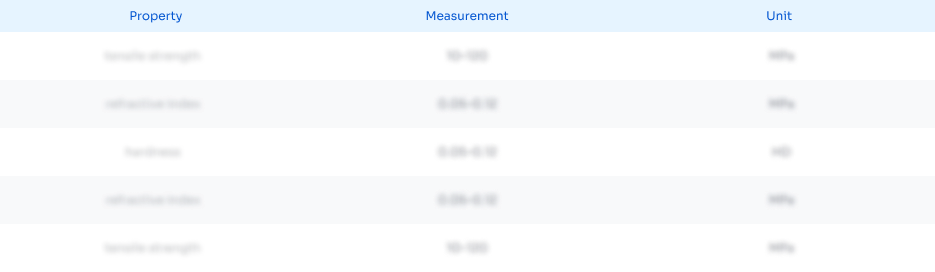
Abstract
Description
Claims
Application Information

- R&D
- Intellectual Property
- Life Sciences
- Materials
- Tech Scout
- Unparalleled Data Quality
- Higher Quality Content
- 60% Fewer Hallucinations
Browse by: Latest US Patents, China's latest patents, Technical Efficacy Thesaurus, Application Domain, Technology Topic, Popular Technical Reports.
© 2025 PatSnap. All rights reserved.Legal|Privacy policy|Modern Slavery Act Transparency Statement|Sitemap|About US| Contact US: help@patsnap.com