Process for preparing brominated polystyrene
A technology for brominated polystyrene and polystyrene, which is applied in the field of preparing brominated polystyrene, can solve the problems of reduced use effect, inconvenient storage and use, etc., and achieves safe and efficient use, easy operation and control, and low price. Effect
- Summary
- Abstract
- Description
- Claims
- Application Information
AI Technical Summary
Problems solved by technology
Method used
Examples
Embodiment 1
[0023] In the 1000 milliliter reaction flask of light-proof, add 400 milliliters of dichloroethanes, polystyrene 50 grams and sulfur 1.8 grams of mass-average molecular weight Mw=25000, stir and drop into bromine 10 grams, keep the material in the reaction flask at 30 around ℃ until the polystyrene melts. Lower the temperature of the material in the reaction flask to 0-2°C, add 2 grams of anhydrous aluminum trichloride powder, and drop in 230 grams of bromine dried by concentrated sulfuric acid within 2 hours. After bromine dripping was completed, the stirring reaction was continued for 2 hours at natural temperature. The reaction product system was washed with 3×300 ml of water, then neutralized with 20% caustic soda aqueous solution with a mass concentration of 20% to neutralize the pH value of the reaction product system to 7.0-7.5, and the water phase was separated. The organic phase was dropped into 1000 ml of methanol, the brominated polystyrene crystallized out was cen...
Embodiment 2
[0025] In a 1000 ml reaction flask protected from light, add 400 ml of dichloroethane and 52 grams of polystyrene with a mass average molecular weight Mw=25000, and keep the material in the reaction flask at around 30° C. until the polystyrene melts. Reduce the material temperature in the reaction flask to 0-2°C, add 1.6 grams of sulfur, 2.3 grams of anhydrous aluminum trichloride powder and 0.3 grams of zinc powder, and drop 235 grams of bromine dried in concentrated sulfuric acid within 2 hours. After bromine dripping was completed, the stirring reaction was continued for 2 hours at natural temperature. The reaction product system was washed with 3×300 ml of water, then neutralized with 20% caustic soda aqueous solution with a mass concentration of 20% to neutralize the pH value of the reaction product system to 7.0-7.5, and the water phase was separated. The organic phase was dropped into 1000 ml of methanol, the crystallized brominated polystyrene was centrifuged to remove...
Embodiment 3
[0027]In a 1000 ml reaction flask protected from light, add 400 ml of dichloroethane and 50 grams of polystyrene with a mass average molecular weight Mw=25000, and keep the material in the reaction flask at around 30° C. until the polystyrene melts. Lower the temperature of the materials in the reaction flask to 0-2°C, add 3.0 grams of sulfur, 3.0 grams of anhydrous aluminum trichloride powder and 0.5 grams of zinc powder, and drop in 250 grams of bromine dried by concentrated sulfuric acid within 2 hours. After bromine dripping was completed, the stirring reaction was continued for 2 hours at natural temperature. The reaction product system was washed with 3×300 ml of water, then neutralized with 20% caustic soda aqueous solution with a mass concentration of 20% to neutralize the pH value of the reaction product system to 7.0-7.5, and the water phase was separated. The organic phase was dropped into 1000 ml of methanol, the crystallized brominated polystyrene was centrifuged ...
PUM
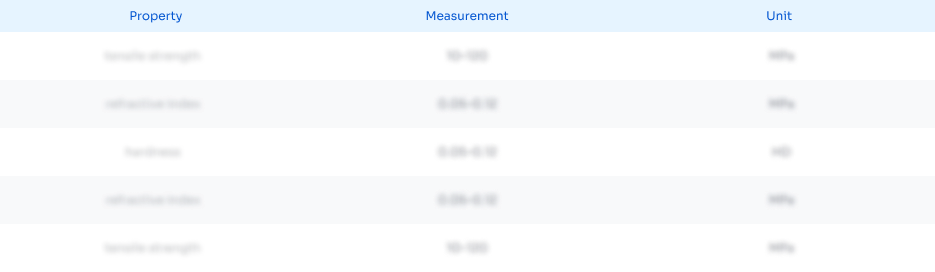
Abstract
Description
Claims
Application Information

- R&D
- Intellectual Property
- Life Sciences
- Materials
- Tech Scout
- Unparalleled Data Quality
- Higher Quality Content
- 60% Fewer Hallucinations
Browse by: Latest US Patents, China's latest patents, Technical Efficacy Thesaurus, Application Domain, Technology Topic, Popular Technical Reports.
© 2025 PatSnap. All rights reserved.Legal|Privacy policy|Modern Slavery Act Transparency Statement|Sitemap|About US| Contact US: help@patsnap.com