Technological process for directly producing spongy iron from high-phosphor oolitic hematite
A technology of oolitic hematite and a process method, which is applied in the direction of improving process efficiency and the like, can solve the problems of high phosphorus content and low iron recovery rate, and achieves the effects of high resource utilization rate, saving cost and shortening process flow
- Summary
- Abstract
- Description
- Claims
- Application Information
AI Technical Summary
Problems solved by technology
Method used
Image
Examples
Embodiment 1
[0008] The raw material is a high-phosphorus oolitic hematite ore containing 28.81% iron and 0.625% phosphorus. The direct reduction roasting conditions are: the amount of reducing agent coal is 20%; the amount of sodium carbonate is 20%; after mixing, reduce and roast in a muffle furnace at 950°C for 35 minutes; cool; grind to a particle size of -0.076 at a grinding concentration of 70% mm accounts for 88%, magnetic separation at a magnetic field strength of 80kA / m. Metal iron powder with iron content of 92.45%, phosphorus content of 0.07%, and other impurity content meeting steelmaking requirements is obtained.
Embodiment 2
[0010] The raw material is a high-phosphorus oolitic hematite ore containing 37.75% iron and 1.03% phosphorus. The direct reduction roasting conditions are: the amount of reducing agent coal is 24%; the amount of sodium carbonate is 24%; after mixing, reduce and roast in a muffle furnace at 1000 ° C for 30 minutes; cool; grind to a particle size of -0.076mm at a concentration of about 78% Accounting for 90%, magnetic separation at a magnetic field strength of 80kA / m. Metal iron powder with an iron content of 91.68%, a phosphorus content of 0.065%, and other impurity contents meeting steelmaking requirements is obtained.
Embodiment 3
[0012] The raw material is a high-phosphorus oolitic hematite ore containing 43.34% iron and 1.36% phosphorus. The direct reduction roasting conditions are: the amount of reducing agent coal is 32%; the amount of sodium carbonate is 30%; after mixing, reduce and roast in a muffle furnace at 900°C for 40 minutes; cool; grind to a particle size of -0.076mm at a concentration of about 75% Accounting for 85%, magnetic separation at a magnetic field strength of 80kA / m. Metal iron powder with an iron content of 91.85%, a phosphorus content of 0.035%, and other impurity contents meeting steelmaking requirements is obtained.
PUM
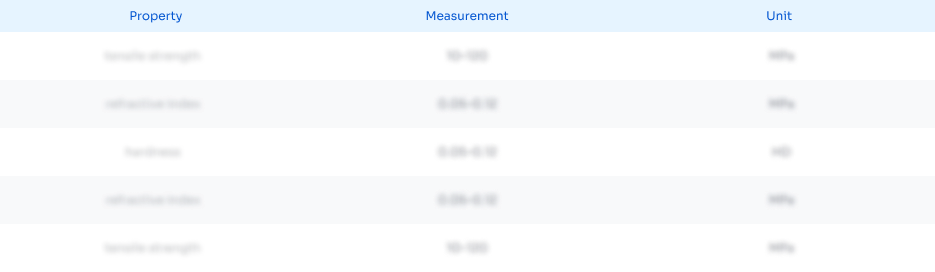
Abstract
Description
Claims
Application Information

- R&D
- Intellectual Property
- Life Sciences
- Materials
- Tech Scout
- Unparalleled Data Quality
- Higher Quality Content
- 60% Fewer Hallucinations
Browse by: Latest US Patents, China's latest patents, Technical Efficacy Thesaurus, Application Domain, Technology Topic, Popular Technical Reports.
© 2025 PatSnap. All rights reserved.Legal|Privacy policy|Modern Slavery Act Transparency Statement|Sitemap|About US| Contact US: help@patsnap.com