Direct-connecting main spindle for multiple-spindle processor
A processing machine, direct connection technology, applied in the direction of metal processing machinery parts, metal processing equipment, manufacturing tools, etc., can solve the problems of increasing the production cost, increasing the production cost, affecting the processing quality, etc., to improve the processing quality and smooth the rotation. Action, cost-saving effect
- Summary
- Abstract
- Description
- Claims
- Application Information
AI Technical Summary
Problems solved by technology
Method used
Image
Examples
Embodiment Construction
[0029] In order to enable your examiner to have a further understanding of the present invention, hereby cite a preferred embodiment and cooperate with the drawings, which are described in detail as follows:
[0030] see figure 2 , image 3 , Figure 4 , Figure 5 As shown, the multi-axis processing machine 20 is provided with a support frame 21 that can be moved up and down, and a plurality of direct-connected spindles 30 are locked on the support frame 21, and each spindle 30 is provided with a long hole 311 The rotating shaft 31, the rotating shaft 31 is provided with a pull rod 32 with a jaw 321 inside to be used for hitting the knife and grabbing the knife, while a detent 33 is sleeved on the outside, and the detent 33 of the detent The bottom is the top spring 34, and the connecting rod 331 penetrates the long hole 311 of the rotating shaft 31 to connect the pull rod 32 to drive the pull rod 32 to move synchronously. Between the pull rods 32 there is a connected kni...
PUM
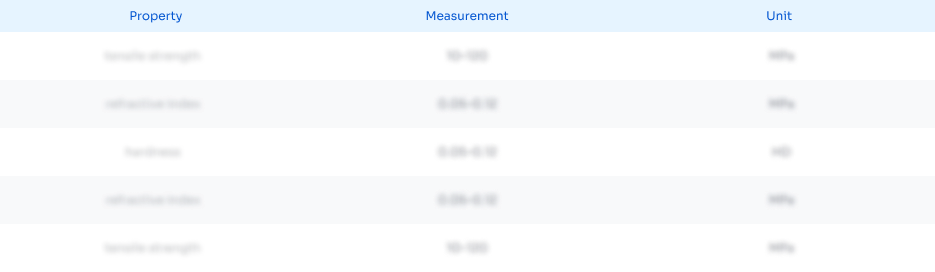
Abstract
Description
Claims
Application Information

- R&D
- Intellectual Property
- Life Sciences
- Materials
- Tech Scout
- Unparalleled Data Quality
- Higher Quality Content
- 60% Fewer Hallucinations
Browse by: Latest US Patents, China's latest patents, Technical Efficacy Thesaurus, Application Domain, Technology Topic, Popular Technical Reports.
© 2025 PatSnap. All rights reserved.Legal|Privacy policy|Modern Slavery Act Transparency Statement|Sitemap|About US| Contact US: help@patsnap.com