Method for extracting noble metal ruthenium from mixed oxide containing ruthenium, iridium, titanium, tin, zirconium and palladium
A mixed oxide and mixed metal technology, applied in the direction of improving process efficiency, can solve the problems of low output and high price, and achieve the effect of saving energy
- Summary
- Abstract
- Description
- Claims
- Application Information
AI Technical Summary
Problems solved by technology
Method used
Examples
Embodiment 1
[0024] Example 1 Recovery of metal anode ruthenium by old diaphragm method
[0025] The old anode was coated with titanium-based ruthenium-titanium-tin oxide to analyze and detect the residual amount of precious metals. Using the non-destructive testing method of X-ray fluorescence detector, the residual amount of ruthenium was measured to be 2.3g / m 2 .
[0026] 1 square meter of the above ruthenium-containing coating was placed in KOH and KNO at a weight ratio of 1:3 3 Dissolve in the molten salt mixture, the dissolution temperature is 400°C, then cool the molten salt, soak in water, filter and separate; add the filtrate to the reaction flask, add sodium hypochlorite containing 10% chlorine to the reaction flask, and the reaction temperature is 60°C , add 40% sulfuric acid after reacting for 5 minutes, the reaction generates ruthenium tetroxide gas, add sodium hypochlorite solution again after adding sodium hypochlorite for 10 minutes for the first time, repeat this step unt...
Embodiment 2
[0028] Embodiment 2 The recovery of old ionic membrane method electrode ruthenium
[0029] The oxide coating of the old anode coating mainly composed of ruthenium, titanium, iridium, zirconium and palladium was analyzed and detected for the residual amount of precious metals, and the residual amount of ruthenium was measured to be 3g / m2 by using the non-destructive testing method of X-ray fluorescence detector. 2 .
[0030] Putting the scrap containing precious metal ruthenium into KOH and KNO at a weight ratio of 1:2 3 Dissolve in the molten salt mixture, the dissolution temperature is 350°C, then cool the molten salt, soak in water, filter and separate; add the filtrate to the reaction flask, add sodium hypochlorite containing 12% chlorine to the reaction flask, and the reaction temperature is 50°C , add 50% sulfuric acid after reacting for 3 minutes, the reaction generates ruthenium tetroxide gas, add sodium hypochlorite solution again after adding sodium hypochlorite for ...
Embodiment 3
[0032] The recovery of the anode ruthenium of embodiment 3 chlorate electrolyzer
[0033] The anode coating containing ruthenium precious metal was analyzed and detected for the residual amount of precious metal, and the residual amount of ruthenium was measured to be 2.53g / m by using the non-destructive testing method of X-ray fluorescence detector. 2 .
[0034] Putting the scrap containing precious metal ruthenium into KOH and KNO at a weight ratio of 1:4 3 Dissolve in the molten salt mixture, the dissolution temperature is 430°C, then cool the molten salt, soak in water, filter and separate; add the filtrate to the reaction flask, add sodium hypochlorite containing 8% chlorine to the reaction flask, and the reaction temperature is 80°C , add 60% sulfuric acid after reacting for 8 minutes, the reaction generates ruthenium tetroxide gas, add sodium hypochlorite solution again after adding sodium hypochlorite for the first time for 15 minutes, repeat this step until the end o...
PUM
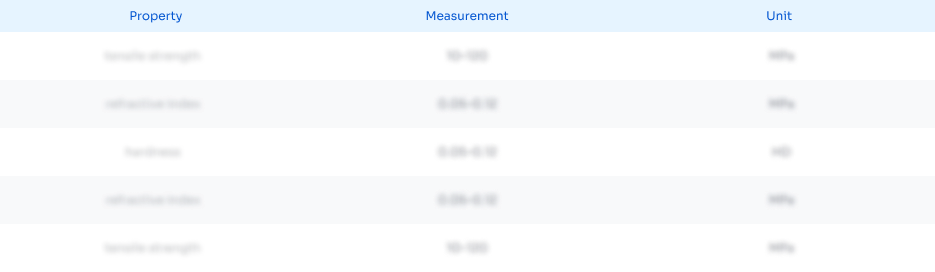
Abstract
Description
Claims
Application Information

- R&D
- Intellectual Property
- Life Sciences
- Materials
- Tech Scout
- Unparalleled Data Quality
- Higher Quality Content
- 60% Fewer Hallucinations
Browse by: Latest US Patents, China's latest patents, Technical Efficacy Thesaurus, Application Domain, Technology Topic, Popular Technical Reports.
© 2025 PatSnap. All rights reserved.Legal|Privacy policy|Modern Slavery Act Transparency Statement|Sitemap|About US| Contact US: help@patsnap.com