Suspended secondary fast reduction process for iron-containing materials and device therefor
A process method and material technology, applied in the field of iron-containing material reduction devices, can solve the problems of low production efficiency, low metallization rate and high cost, and achieve the effects of high production capacity, large mass transfer coefficient and small footprint
- Summary
- Abstract
- Description
- Claims
- Application Information
AI Technical Summary
Problems solved by technology
Method used
Image
Examples
Embodiment 1
[0039] Iron-containing materials: iron ore fine powder; reducing gas: generating gas.
[0040] The process flow of the gas suspension reduction system for iron-containing materials is as follows: figure 1 shown. Iron-containing materials and fine powder materials with a lime particle size range of 1-40 μm are sent from the lifting device 1 to the first-stage heat exchange tube 2, and after fully exchanging heat with the high-temperature reducing gas from the second-stage cyclone preheater 5, they enter the first-stage cyclone Preheater 3; in the first-stage cyclone preheater 3, the suspended iron-containing material particles are separated from the reducing gas and then enter the second-stage heat exchange tube 4, and the gas passes through the fan 17, the dust collector 18, and the waste reducing gas collection system 19 collection, the outlet temperature of the waste reducing gas is 150-300°C; the preheated iron-containing material enters the II-stage heat exchange tube 4, ...
Embodiment 2
[0042] Iron-containing materials: 80% iron ore fine powder, 20% iron-containing metallurgical dust; reducing gas: coke oven gas.
[0043] Such as figure 2 As shown, the coke oven gas enters the gas tank 23 after being preheated by the preheater 26 . The coke oven gas from the coke oven gas preheater 26 replaces the generated gas from the gas generator 25 . The cross section of the heat exchange tubes of the cyclone preheater is circular. Others are the same as embodiment 1.
Embodiment 3
[0045] Iron-containing material: 10%-90% of iron ore fine powder, 90%-10% of iron-containing metallurgical dust; reducing gas: natural gas, which replaces the coke oven gas in Example 2 with natural gas. Others are with embodiment 2.
PUM
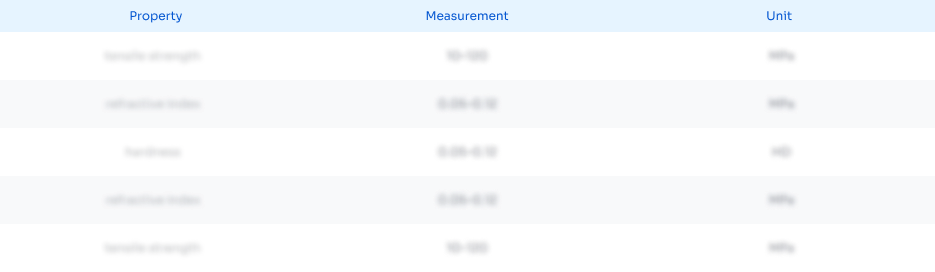
Abstract
Description
Claims
Application Information

- R&D
- Intellectual Property
- Life Sciences
- Materials
- Tech Scout
- Unparalleled Data Quality
- Higher Quality Content
- 60% Fewer Hallucinations
Browse by: Latest US Patents, China's latest patents, Technical Efficacy Thesaurus, Application Domain, Technology Topic, Popular Technical Reports.
© 2025 PatSnap. All rights reserved.Legal|Privacy policy|Modern Slavery Act Transparency Statement|Sitemap|About US| Contact US: help@patsnap.com