Copolymer of fibroin and poly D,L-lactic acid, preparation method and application thereof
A silk protein and copolymer technology, applied in the field of silk protein and poly-D, can solve the problem of no research report
- Summary
- Abstract
- Description
- Claims
- Application Information
AI Technical Summary
Problems solved by technology
Method used
Image
Examples
Embodiment 1
[0056] D, L-lactide, dehydrated silk protein powder (number average relative molecular mass 3000), SnCl 2 / p-toluenesulfonic acid catalyst system (SnCl 2 The molar content accounts for 50% of the whole catalyst system) into the polymerization tank. SnCl 2 The dosage is 0.5wt% of D, L-lactide, and the mass ratio of D, L-lactide to silk protein is 4:1. The pressure of the system was gradually reduced to 0 mmHg (manometer reading) and then sealed, the reaction temperature was 170° C., and the reaction time was 10 hours. After the polymerization, the obtained copolymer was dissolved in ethyl acetate, filtered and precipitated with ether, and the filtered precipitate was vacuum-dried at 65° C. for 16 hours to obtain a purified silk protein and poly D, L-lactic acid copolymer. After purification, the copolymer is a yellow powder with a molecular weight of 12,000, a yield of 75%, and no melting point.
Embodiment 2
[0058] D, L-lactide, silk fibroin protein powder (the number average relative molecular mass is 3000), SnCl 2 / naphthalenesulfonic acid catalyst system (SnCl 2 The molar content accounts for 50% of the whole catalyst system) into the polymerization tank. SnCl 2 The dosage is 0.5wt% of D, L-lactide, and the mass ratio of D, L-lactide to silk protein is 10:1. The pressure of the system was gradually reduced to 10 mm Hg and then sealed, the reaction temperature was 170° C., and the reaction time was 10 hours. After the polymerization was complete, the resulting copolymer was dissolved in ethyl acetate, filtered and precipitated with diethyl ether. The filtered precipitate was vacuum-dried at 65° C. for 16 hours to obtain a purified polylactic acid and silk fibroin peptide chain copolymer. The purified copolymer is a yellow powder with a molecular weight of 16,300, a yield of 73%, and a melting point of 120°C.
Embodiment 3
[0060] Add D, L-lactide, silk fibroin protein powder (the number-average relative molecular mass is 1000), stannous octoate / naphthalenesulfonic acid catalyst system (the molar content of stannous octoate accounts for 50% of the entire catalyst system) into the polymerization kettle middle. The dosage of stannous octoate is 0.5wt% of D, L-lactide, and the mass ratio of D, L-lactide to silk protein is 10:1. The pressure of the system was gradually reduced to 2 mm Hg and then sealed, the reaction temperature was 170° C., and the reaction time was 15 hours. After the polymerization was complete, the resulting copolymer was dissolved in ethyl acetate, filtered and precipitated with diethyl ether. The filtered precipitate was vacuum-dried at 65° C. for 10 hours to obtain a copolymer of purified silk protein and poly-D, L-lactic acid. The purified copolymer is a yellow powder with a molecular weight of 18,000, a yield of 76%, and a melting point of 130°C.
PUM
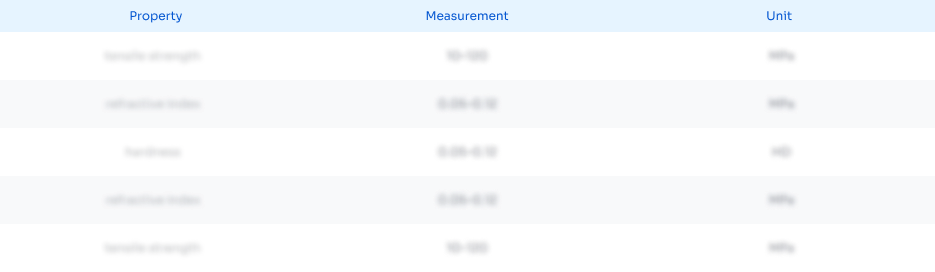
Abstract
Description
Claims
Application Information

- R&D
- Intellectual Property
- Life Sciences
- Materials
- Tech Scout
- Unparalleled Data Quality
- Higher Quality Content
- 60% Fewer Hallucinations
Browse by: Latest US Patents, China's latest patents, Technical Efficacy Thesaurus, Application Domain, Technology Topic, Popular Technical Reports.
© 2025 PatSnap. All rights reserved.Legal|Privacy policy|Modern Slavery Act Transparency Statement|Sitemap|About US| Contact US: help@patsnap.com