Method for infiltrating tungsten carbide on the surface of carbon material
A technology of carbon material and tungsten carbide, which is applied in the field of tungsten carbide to achieve the effects of alleviating thermal mismatch, simple process and improving adhesion
- Summary
- Abstract
- Description
- Claims
- Application Information
AI Technical Summary
Problems solved by technology
Method used
Examples
Embodiment 1
[0013] The carbon-based tungsten coating prepared by PVD method is put into a heat treatment furnace for high temperature heat treatment. The heat treatment process is as follows: first raise the temperature to 1050°C, keep it warm for 2.5 hours, then continue to raise the temperature to 1300°C and keep it warm for 1.5 hours, then cool with the furnace. Repeat the above deposition and heat treatment process 3 times, 50 μm deep tungsten carbide is infiltrated on the surface of the carbon material, and the tungsten carbide content reaches 5%.
Embodiment 2
[0015] Put the carbon-based tungsten coating prepared by CVD into a heat treatment furnace for high temperature heat treatment. The heat treatment process is as follows: first raise the temperature to 1100°C, keep it warm for 2 hours, then continue to raise the temperature to 1350°C and keep it warm for 1 hour, then cool with the furnace. Repeat the above deposition and heat treatment process for 4 times, 100 μm deep tungsten carbide is infiltrated on the surface of the carbon material, and the tungsten carbide content reaches 12%.
Embodiment 3
[0017] Put the carbon-based tungsten coating prepared by the DGP method into a heat treatment furnace for high temperature heat treatment. The heat treatment process is as follows: first raise the temperature to 1150°C, keep it warm for 1.5 hours, then continue to raise the temperature to 1400°C and keep it warm for 0.5 hour, then cool with the furnace. Repeat the above deposition and heat treatment process for 5 times, 300 μm deep tungsten carbide is infiltrated on the surface of the carbon material, and the tungsten carbide content reaches 19%.
PUM
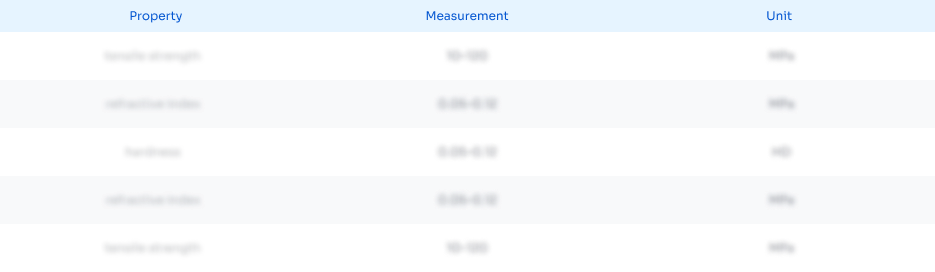
Abstract
Description
Claims
Application Information

- R&D
- Intellectual Property
- Life Sciences
- Materials
- Tech Scout
- Unparalleled Data Quality
- Higher Quality Content
- 60% Fewer Hallucinations
Browse by: Latest US Patents, China's latest patents, Technical Efficacy Thesaurus, Application Domain, Technology Topic, Popular Technical Reports.
© 2025 PatSnap. All rights reserved.Legal|Privacy policy|Modern Slavery Act Transparency Statement|Sitemap|About US| Contact US: help@patsnap.com