Leather-like sheet
A sheet and leather technology, used in transportation and packaging, textiles and papermaking, thin material processing, etc., can solve the problems of difficulty in obtaining soft leather-like sheets, no records, etc., and achieve excellent surface quality, durability and resistance. The effect of excellent flexibility and soft touch
- Summary
- Abstract
- Description
- Claims
- Application Information
AI Technical Summary
Problems solved by technology
Method used
Image
Examples
Embodiment
[0152] Hereinafter, the present invention will be described in more detail with reference to examples.
[0153] [Measuring method of number average molecular weight (Mn)]
[0154] It measured using the gel permeation chromatography (GPC) method, and calculated|required the number average molecular weight (Mn) by polystyrene conversion.
[0155] [Measuring method of melt viscosity]
[0156] The melt viscosity (mPa·s) of the urethane prepolymer was measured using a cone and plate viscometer (manufactured by ICI Corporation, measuring temperature: 125° C.).
[0157] [Measurement method of glass transition temperature (Tg)]
[0158] The glass transition temperature (Tg) of the urethane prepolymer is obtained by coating the urethane prepolymer to a thickness of 150 μm, aging it for 5 days at an ambient temperature of 23°C and a relative humidity of 65%, and then using a dynamic adhesive The film was measured with an elastic measuring device (manufactured by Rheometric, frequency...
Synthetic example 1
[0180] The alkylene oxide adduct of bisphenol A obtained by adding 6 mol of propylene oxide on 1 mol of bisphenol A reacts with sebacic acid and isophthalic acid to obtain a polyester polyol (I) with a number average molecular weight of 2000 .
[0181] In a 1L four-necked flask, at 120°C, 50 parts by mass of polytetramethylene glycol with a number average molecular weight of 2000 and 50 parts by mass of the polyester polyol (I) synthesized above were heated under reduced pressure to dehydrate them. to a moisture content of 0.05% by mass.
[0182] Next, in the above-mentioned mixture of polytetramethylene glycol and polyester polyol (I) cooled to 60°C, add 20 parts by mass of 4,4'-diphenylmethane diisocyanate, and then add 0.01 part by mass of diphenylmethane diisocyanate Butyltin dilaurate was used as a catalyst, and then the temperature was raised to 110° C., and the reaction was carried out for 5 hours until the content of isocyanate groups was constant to obtain a urethane...
Synthetic example 2
[0184] In 100 parts by mass of the above-mentioned urethane prepolymer (1) heated to 110°C, add 0.68 parts by mass of 2-hydroxyethyl acrylate and 0.01 part by mass of tin octoate to react to obtain the urethane prepolymer (2 ). The ratio ([HEA / NCO]×100) of the number of isocyanate groups reacted with the hydroxyl groups of 2-hydroxyethyl acrylate to the total number of isocyanate groups in the urethane prepolymer (1) was 10%.
[0185] In addition, ([HEA / NCO]×100) of the above-mentioned urethane prepolymer (2) was calculated|required by the following method. An excess amount of dibutylamine is added to the urethane prepolymer (2), and the remaining isocyanate groups in the urethane prepolymer (2) are reacted with dibutylamine. Next, the amount of the remaining dibutylamine was determined by back titration using hydrochloric acid, thereby calculating the amount of isocyanate groups contained in the urethane prepolymer (2). ([HEA / NCO]×100) of the urethane prepolymers (3) to (12...
PUM
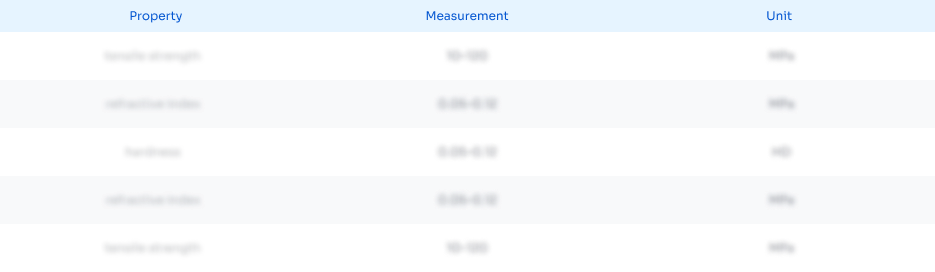
Abstract
Description
Claims
Application Information

- Generate Ideas
- Intellectual Property
- Life Sciences
- Materials
- Tech Scout
- Unparalleled Data Quality
- Higher Quality Content
- 60% Fewer Hallucinations
Browse by: Latest US Patents, China's latest patents, Technical Efficacy Thesaurus, Application Domain, Technology Topic, Popular Technical Reports.
© 2025 PatSnap. All rights reserved.Legal|Privacy policy|Modern Slavery Act Transparency Statement|Sitemap|About US| Contact US: help@patsnap.com