Preparation technique of catalysis type composite curing agent in composite wear-resistant coating material
A composite curing agent and wear-resistant coating technology, applied in coatings, epoxy resin coatings, etc., can solve the problems of incomplete curing of composite materials, high toxicity in the construction environment, low cross-linking density, etc., to reduce internal stress, Excellent wear resistance and good adhesion
- Summary
- Abstract
- Description
- Claims
- Application Information
AI Technical Summary
Problems solved by technology
Method used
Examples
Embodiment 1
[0018] The invention discloses a preparation process suitable for a catalytic composite curing agent in a composite wear-resistant coating material. The catalytic composite curing agent includes an amine catalytic composite curing agent, and the amine catalytic composite curing agent is specifically prepared The method is: first select aromatic polyamines, 2-ethyl-4-methylimidazole, resorcinol, salicylic acid and 2,4,6-tris(dimethylaminomethyl)phenol for standby, and then use aromatic Polymerization modification treatment of polyamines, finally the aromatic polyamines modified by addition polymerization accounted for 65-85%, 2-ethyl-4-methylimidazole accounted for 5-15%, and resorcinol accounted for 5%. ~15%, salicylic acid accounts for 0~5%, and 2,4,6-tris(dimethylaminomethyl)phenol accounts for 0~5%, select at least three of them for compatibility, and mechanically stir and mix evenly according to the mass percentage , forming an amine-catalyzed composite curing agent. The ...
Embodiment 2
[0020] As another preferred embodiment of the present invention, the catalytic composite curing agent also includes an acid anhydride catalytic composite curing agent, and the specific preparation method of the acid anhydride catalytic composite curing agent is: select an organic mixed anhydride and benzyl dimethylamine The organic mixed acid anhydride accounts for 95-99% and the benzyl dimethylamine accounts for 1-5%, and mechanically stirs and mixes uniformly according to the mass percentage to form an acid anhydride catalytic type composite curing agent.
Embodiment 3
[0022] On the basis of Example 2, another preferred embodiment of the present invention, wherein the organic mixed acid anhydride accounts for 30-55% of phthalic anhydride, 20-30% of hexahydrophthalic anhydride, formic Methyl tetrahydrophthalic anhydride accounts for 15-35%, and methyl hexahydrophthalic anhydride accounts for 0-20%. At least three of the above-mentioned raw materials are mixed each time, and mechanically stirred and mixed according to the mass percentage to form uniformly.
PUM
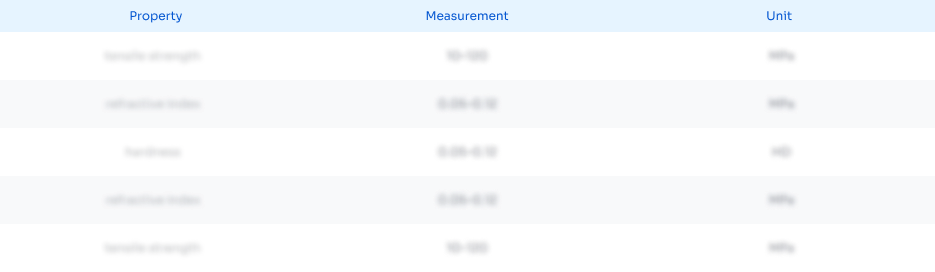
Abstract
Description
Claims
Application Information

- Generate Ideas
- Intellectual Property
- Life Sciences
- Materials
- Tech Scout
- Unparalleled Data Quality
- Higher Quality Content
- 60% Fewer Hallucinations
Browse by: Latest US Patents, China's latest patents, Technical Efficacy Thesaurus, Application Domain, Technology Topic, Popular Technical Reports.
© 2025 PatSnap. All rights reserved.Legal|Privacy policy|Modern Slavery Act Transparency Statement|Sitemap|About US| Contact US: help@patsnap.com