Method for distillation separation of mixture of nervonic acid and erucic acid from acer truncatum oil
A technology of distillation separation and molecular distillation, which is applied in the separation/purification of carboxylic acid compounds, chemical instruments and methods, and the preparation of organic compounds, etc. It can solve the problems of many stages of molecular distillation, high distillation temperature, and low resource utilization , to achieve the effects of low operating temperature, favorable absorption and utilization, and fewer stages of molecular distillation
- Summary
- Abstract
- Description
- Claims
- Application Information
AI Technical Summary
Problems solved by technology
Method used
Examples
Embodiment 1
[0025] (1) 500 grams of maple ingot seeds are crushed and loaded into the extractor, the supercritical carbon dioxide extraction temperature is 45° C., the pressure is 30 MPa, the separation temperature is 60° C., and the pressure is 8 MPa to obtain 60 grams of maple ingot oil;
[0026] (2) After mixing 20 milliliters of absolute ethanol with 40 milliliters of ingot maple oil, add 2 grams of NaOH, and react for 2 hours at a temperature of 70 ° C. After the product is separated from glycerin, the catalyst is eluted with water, and unreacted ethanol is removed by distillation to obtain Ingot Maple Oil Ethyl Ester 30ml;
[0027] (3) Separation of erucic acid and ethyl nervate: Carry out two-stage molecular distillation under different vacuum degree and temperature conditions to the prepared ingot maple oil ethyl ester, the first stage, vacuum degree 0.2Pa, temperature 136 ℃, light Components enter the second stage of molecular distillation with a vacuum of 6 Pa and a temperature ...
Embodiment 2
[0030] (1) 5000 grams of maple ingot seeds are crushed to obtain 480 grams of maple ingot oil by pressing;
[0031] (2) After mixing 20 milliliters of absolute ethanol with 120 milliliters of ingot maple oil, add 8 grams of KOH, and react for 1 hour at a temperature of 76 ° C. After the product is separated from glycerin, the catalyst is eluted with water, and unreacted ethanol is removed by distillation to obtain Yuanbao Maple Oil Ethyl Ester 92ml;
[0032] (3) Separation of erucic acid and ethyl nervate: Carry out two-stage molecular distillation under different vacuum degree and temperature conditions to the prepared ingot maple oil ethyl ester, the first stage, vacuum degree 0.8Pa, temperature 143 ℃, light Components enter the second stage of molecular distillation with a vacuum of 8Pa and a temperature of 125°C. The heavy fractions of the second stage of molecular distillation are collected and analyzed by gas chromatography. The content of ethyl neurate is 36%, and the c...
Embodiment 3
[0035] (1) 500 grams of maple ingot seeds are pulverized and extracted with No. 6 solvent oil to obtain 70 grams of maple ingot oil;
[0036] (2) 20 milliliters of absolute ethanol containing 2% sodium ethylate was mixed with 20 milliliters of ingot maple oil, and reacted for 5 hours when the temperature was 50° C. After the product was separated from glycerin, the catalyst was eluted with water, and unreacted ethanol was removed by distillation. Obtain 15 ml of ingot maple oil ethyl ester;
[0037] (3) Separation of erucic acid and ethyl nervate: Carry out two-stage molecular distillation under different vacuum degree and temperature conditions to the prepared ingot maple oil ethyl ester, the first stage, vacuum degree 0.5Pa, temperature 140 ℃, light Components enter the second-stage molecular distillation with a vacuum of 6 Pa and a temperature of 128°C. The heavy fractions of the second-stage molecular distillation are collected and analyzed by gas chromatography. The conte...
PUM
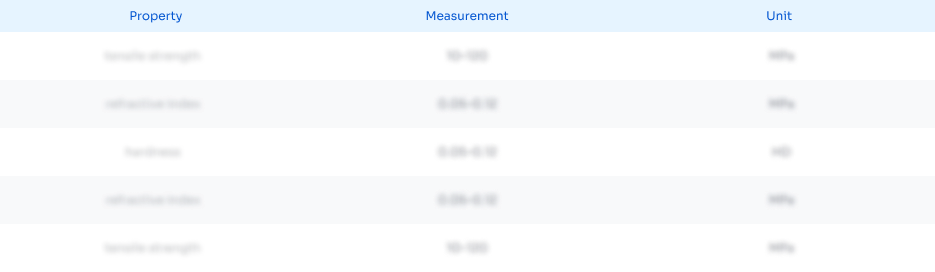
Abstract
Description
Claims
Application Information

- R&D Engineer
- R&D Manager
- IP Professional
- Industry Leading Data Capabilities
- Powerful AI technology
- Patent DNA Extraction
Browse by: Latest US Patents, China's latest patents, Technical Efficacy Thesaurus, Application Domain, Technology Topic, Popular Technical Reports.
© 2024 PatSnap. All rights reserved.Legal|Privacy policy|Modern Slavery Act Transparency Statement|Sitemap|About US| Contact US: help@patsnap.com