Method for preparing aromatic-aliphatic copolyester
An aliphatic copolyester and aromatic technology, which is applied in the field of preparing degradable aromatic-aliphatic copolyester, can solve the problems of easy pollution of the environment, not a synthetic process method, and difficult degradation, so as to reduce the sequence length, Good mechanical behavior, cheap and easy-to-obtain raw materials
- Summary
- Abstract
- Description
- Claims
- Application Information
AI Technical Summary
Problems solved by technology
Method used
Image
Examples
Embodiment 1
[0015] 4.15g (0.025mol) terephthalic acid, 9.01g (0.1mol) 1,4-butanediol and 3wt% Ti[OBu] 4 Add it into a 50ml flask, stir it under normal pressure at 200°C for 1 hour, then raise the temperature to 210°C, stir it under normal pressure for 0.5 hour, then stir it under normal pressure at 220°C for 0.5 hour, keep the temperature constant and lower the pressure to 20000Pa, continue After 3 hours of reaction, dibutylene terephthalate can be obtained.
[0016] Add 3.45g of polylactic acid prepolymer (obtained by direct dehydration of lactic acid at 150°C, the amount of lactic acid is 0.0083mol) to dibutylene terephthalate, gradually reduce the pressure to 50Pa at 230°C, and stir for 6h. A degradable copolyester is obtained.
Embodiment 2
[0018] 4.15g (0.025mol) terephthalic acid, 7.20g (0.08mol) 1,4-butanediol, 2.88g (0.02mol) cyclohexanedimethanol and 5wt% Ti[OBu] 4 Add it into a 50ml flask, stir it under normal pressure at 210°C for 1 hour, then raise the temperature to 220°C, stir it under normal pressure for 0.5 hour, then stir it under normal pressure at 230°C for 0.5 hour, keep the temperature constant and lower the pressure to 20000Pa, continue After 4 hours of reaction, dibutylene terephthalate can be obtained.
[0019] Add 3.45g of polylactic acid prepolymer (obtained by direct dehydration of lactic acid at 150°C, the amount of lactic acid is 0.0083mol) to dibutylene glycol cyclohexanedimethanol terephthalate, and gradually reduce the pressure to 50Pa at 250°C , stirring for 6 hours to obtain a degradable copolyester.
Embodiment 3
[0021] With 4.15g (0.025mol) terephthalic acid, 10.61g (0.1mol) diethylene glycol and 3wt% Ti[OBu] 4 Add it into a 50ml flask, stir it under normal pressure at 200°C for 1 hour, then raise the temperature to 210°C, stir it under normal pressure for 0.5 hour, then stir it under normal pressure at 220°C for 0.5 hour, keep the temperature constant and lower the pressure to 20000Pa, continue After 3 hours of reaction, dibutylene terephthalate can be obtained.
[0022] Add 3.45g of polylactic acid prepolymer (obtained by direct dehydration of lactic acid at 150°C, the amount of lactic acid is 0.0083mol) to dibutylene terephthalate, gradually reduce the pressure to 50Pa at 230°C, and stir for 6h. A degradable copolyester is obtained.
PUM
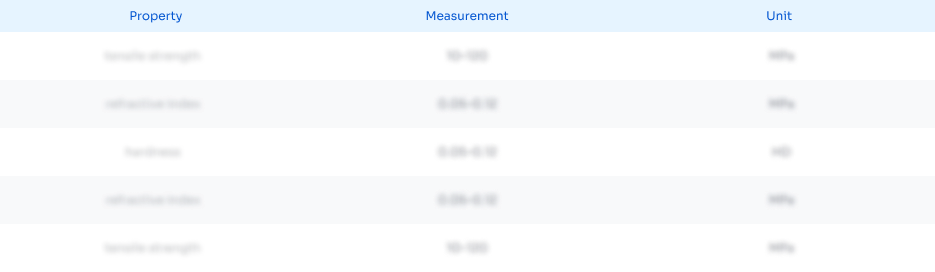
Abstract
Description
Claims
Application Information

- R&D Engineer
- R&D Manager
- IP Professional
- Industry Leading Data Capabilities
- Powerful AI technology
- Patent DNA Extraction
Browse by: Latest US Patents, China's latest patents, Technical Efficacy Thesaurus, Application Domain, Technology Topic, Popular Technical Reports.
© 2024 PatSnap. All rights reserved.Legal|Privacy policy|Modern Slavery Act Transparency Statement|Sitemap|About US| Contact US: help@patsnap.com