Method for improving baking finish hardenability of AA6022 aluminum alloy sheet
A technology of aluminum alloy plate and paint hardening, which is applied in the field of aluminum alloy heat treatment, can solve the problems of low strength, achieve the effects of impact resistance, broad market prospect, and increase the stamping yield
- Summary
- Abstract
- Description
- Claims
- Application Information
AI Technical Summary
Problems solved by technology
Method used
Image
Examples
Embodiment 1
[0017] The alloy composition is 1.25% Si, 0.48% Mg, 0.02% Cu, 0.1% Mn, 0.12% Fe, 0.1% Cr, 0.25% Zn, 0.15% Ti, and the balance is Al AA6022 aluminum alloy ingot in terms of mass percentage, After homogenization treatment at 480°C×8h+550°C×12h in a circulating air furnace, head cutting, face milling, hot rolling and finally cold rolling to a 1mm thin plate; the thin plate is water quenched after solution treatment at 550°C×1h, room temperature After parking for 10 hours, conduct heat treatment at 75°C×8h in a circulating air furnace, and then perform tensile and cupping tests after parking at room temperature for 1 month. The simulated 175°C×30min baking paint heat treatment is carried out in an oil bath furnace of.
Embodiment 2
[0019] The alloy composition is 1.25% Si, 0.48% Mg, 0.02% Cu, 0.1% Mn, 0.12% Fe, 0.1% Cr, 0.25% Zn, 0.15% Ti, and the balance is Al AA6022 aluminum alloy ingot in terms of mass percentage, After homogenization treatment at 480°C×8h+550°C×12h in a circulating air furnace, head cutting, face milling, hot rolling and finally cold rolling to a thin plate of 1mm; the thin plate is water quenched after solution treatment at 550°C×1h, Immediately conduct heat treatment at 70°C x 30min in a circulating air furnace, and then perform tensile and cupping tests after parking at room temperature for 1 month. The simulated 175°C x 30min baking paint heat treatment is carried out in an oil bath furnace.
Embodiment 3
[0021] The alloy composition is 1.25% Si, 0.48% Mg, 0.02% Cu, 0.1% Mn, 0.12% Fe, 0.1% Cr, 0.25% Zn, 0.15% Ti, and the balance is Al AA6022 aluminum alloy ingot in terms of mass percentage, After homogenization treatment at 480°C×8h+550°C×12h in a circulating air furnace, head cutting, face milling, hot rolling and finally cold rolling to a 1mm thin plate; the thin plate is water quenched after solution treatment at 550°C×1h, room temperature After parking for 3 days, conduct heat treatment at 100°C×6h in a circulating air furnace, and then perform tensile and cupping tests after parking at room temperature for 1 month, simulating 175°C×30min baking paint heat treatment is carried out in an oil bath furnace of.
PUM
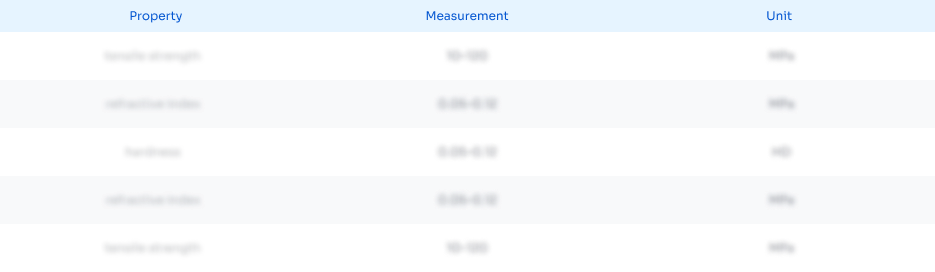
Abstract
Description
Claims
Application Information

- R&D
- Intellectual Property
- Life Sciences
- Materials
- Tech Scout
- Unparalleled Data Quality
- Higher Quality Content
- 60% Fewer Hallucinations
Browse by: Latest US Patents, China's latest patents, Technical Efficacy Thesaurus, Application Domain, Technology Topic, Popular Technical Reports.
© 2025 PatSnap. All rights reserved.Legal|Privacy policy|Modern Slavery Act Transparency Statement|Sitemap|About US| Contact US: help@patsnap.com