Preparation of carbon/carbon composite material molybdenum disilicide outer coating
A carbon composite material, molybdenum disilicide technology, applied in the field of preparation of molybdenum disilicide outer coating, can solve the problems of high reaction temperature, easy peeling off of the coating, complex structure, etc., and achieve dense and uniform structure, short reaction cycle, internal The effect of less stress
- Summary
- Abstract
- Description
- Claims
- Application Information
AI Technical Summary
Problems solved by technology
Method used
Image
Examples
Embodiment 1
[0016] Example 1: Select commercially available molybdenum disilicide powder with an average particle size of 180 meshes, elemental iodine with a purity ≥ 99.7%, and isopropanol with a purity ≥ 99.8% as raw materials: first wet the molybdenum disilicide powder after ball milling for 10 hours Add 1g into the Erlenmeyer flask, then pour 250ml of isopropanol into the Erlenmeyer flask to obtain a suspension, then put the suspension into a 300W ultrasonic generator and vibrate for 30min, then stir on a magnetic stirrer for 12h to obtain suspension A Add 0.05g of iodine elemental substance to the suspension A, put it into a 300W ultrasonic generator and vibrate for 30min, take it out and stir it on a magnetic stirrer for 12h to make solution B; pour the above solution B into the hydrothermal reaction kettle , the filling degree is controlled at 70%; then the carbon / carbon composite material sample with SiC inner coating is clamped on the cathode clamp in the hydrothermal kettle, and ...
Embodiment 2
[0017] Example 2: Select commercially available molybdenum disilicide powder with an average particle size of 180 meshes, elemental iodine with a purity ≥ 99.7%, and isopropanol with a purity ≥ 99.8% as raw materials: first wet the molybdenum disilicide powder after ball milling for 20 hours Add 2g into the Erlenmeyer flask, then pour 200ml of isopropanol into the Erlenmeyer flask to obtain a suspension, then put the suspension into a 250W ultrasonic generator and vibrate for 50min, then stir on a magnetic stirrer for 16h to obtain suspension A ; Add 0.2g of iodine elemental substance to the suspension A, put it into a 250W ultrasonic generator and vibrate for 50min, take it out and stir it on a magnetic stirrer for 16h to obtain a solution B; pour the above solution B into a hydrothermal reaction kettle , the filling degree is controlled at 65%; then the carbon / carbon composite material sample with SiC inner coating is clamped on the cathode clamp in the hydrothermal kettle, a...
Embodiment 3
[0018] Example 3: Select commercially available molybdenum disilicide powder with an average particle size of 180 meshes, elemental iodine with a purity ≥ 99.7%, and isopropanol with a purity ≥ 99.8% as raw materials: first, molybdenum disilicide powder after wet ball milling for 30 hours Add 5g into the Erlenmeyer flask, then pour 150ml of isopropanol into the Erlenmeyer flask to obtain a suspension, then put the suspension into a 230W ultrasonic generator and vibrate for 40min, then stir on a magnetic stirrer for 20h to obtain suspension A ; Add 0.1g of iodine elemental substance to the suspension A, put it into a 230W ultrasonic generator and vibrate for 40min, take it out and put it on a magnetic stirrer to stir for 20h to obtain a solution B; pour the above solution B into a hydrothermal reaction kettle In the process, the filling degree is controlled at 72%; then the carbon / carbon composite material sample with SiC inner coating is clamped on the cathode clamp in the hydr...
PUM
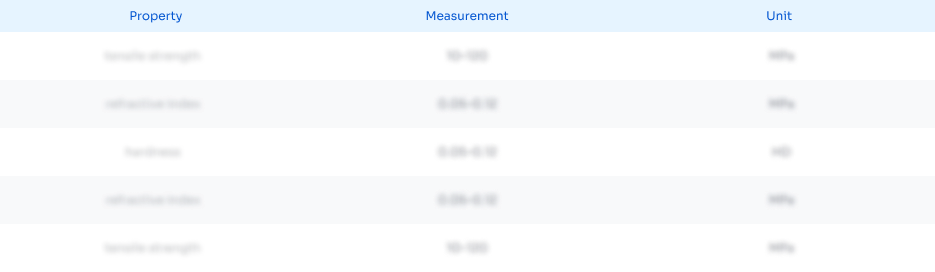
Abstract
Description
Claims
Application Information

- Generate Ideas
- Intellectual Property
- Life Sciences
- Materials
- Tech Scout
- Unparalleled Data Quality
- Higher Quality Content
- 60% Fewer Hallucinations
Browse by: Latest US Patents, China's latest patents, Technical Efficacy Thesaurus, Application Domain, Technology Topic, Popular Technical Reports.
© 2025 PatSnap. All rights reserved.Legal|Privacy policy|Modern Slavery Act Transparency Statement|Sitemap|About US| Contact US: help@patsnap.com