Direct frequency-output vibration gyroscope structure
A technology of output frequency, vibrating gyroscope, applied in the direction of gyro effect for speed measurement, gyroscope/steering induction equipment, piezoelectric effect/electrostrictive or magnetostrictive motor, etc., to improve sensitivity and measurement accuracy, suppress common The effect of mode interference and anti-interference ability enhancement
- Summary
- Abstract
- Description
- Claims
- Application Information
AI Technical Summary
Problems solved by technology
Method used
Image
Examples
Embodiment Construction
[0015] Such as figure 1 As shown, the vibrating gyroscope structure of the direct output frequency of the present invention comprises a mass block 1, a first elastic support 2, a second elastic support 3, a third elastic support 4 and a fourth elastic support 5, and the first vertical outward deviation is 5° The support arm 6, the second vertically deflected 5° support arm 7, the third vertically deflect 5° support arm 8, the fourth vertically deflect 5° support arm 9, the first resonant beam 10 and the second resonant beam 11. The mass block 1 forms a first-order resonance system with the first elastic support 2, the second elastic support 3, the third elastic support 4 and the fourth elastic support 5. The four supports are all placed horizontally. The first elastic support 2 and the second elastic support The support 3 is connected to the center of the top of the mass block 1 , and the third elastic support 4 and the fourth elastic support 5 are connected to the center of ...
PUM
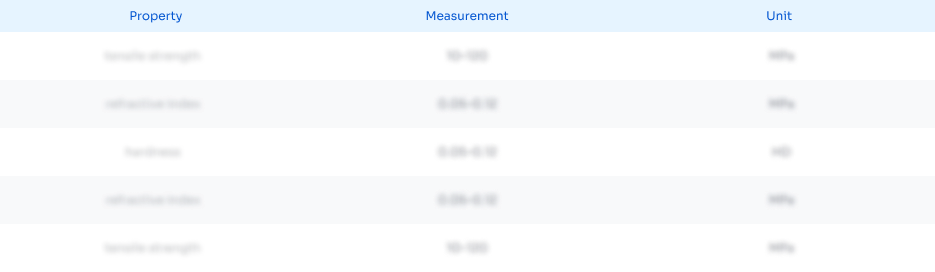
Abstract
Description
Claims
Application Information

- R&D
- Intellectual Property
- Life Sciences
- Materials
- Tech Scout
- Unparalleled Data Quality
- Higher Quality Content
- 60% Fewer Hallucinations
Browse by: Latest US Patents, China's latest patents, Technical Efficacy Thesaurus, Application Domain, Technology Topic, Popular Technical Reports.
© 2025 PatSnap. All rights reserved.Legal|Privacy policy|Modern Slavery Act Transparency Statement|Sitemap|About US| Contact US: help@patsnap.com