Method for manufacturing contact window for reducing contact resistance
A manufacturing method and contact resistance technology, applied in semiconductor/solid-state device manufacturing, circuits, electrical components, etc., can solve problems affecting process reliability and component performance, eroding borophosphosilicate glass layers, etc., to prevent expansion and avoid excessive The effect of erosion
- Summary
- Abstract
- Description
- Claims
- Application Information
AI Technical Summary
Problems solved by technology
Method used
Image
Examples
Embodiment Construction
[0061] Figure 2A to Figure 2C is a schematic cross-sectional view of the manufacturing process of the contact window according to an embodiment of the present invention.
[0062] Please refer to Figure 2A , providing a substrate 200, which is, for example, a silicon substrate. A gate structure 220 has been formed on the substrate 200 . The gate structure 220 may be a gate structure in a dynamic random access memory (DRAM), a gate structure in a metal oxide semiconductor (MOS), or a gate structure in other semiconductor devices, The present invention is not particularly limited. In this embodiment, the gate structure 220 is composed of, for example, a floating gate 220a, a control gate 220b, an inter-gate dielectric layer 220c, a tunnel dielectric layer 220d, and a top cap layer 220e. The material of the floating gate 220 a and the control gate 220 b is, for example, a doped polysilicon layer, and the formation method thereof is, for example, chemical vapor deposition. T...
PUM
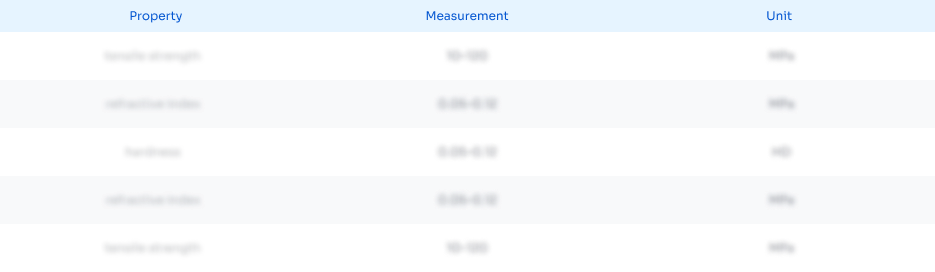
Abstract
Description
Claims
Application Information

- Generate Ideas
- Intellectual Property
- Life Sciences
- Materials
- Tech Scout
- Unparalleled Data Quality
- Higher Quality Content
- 60% Fewer Hallucinations
Browse by: Latest US Patents, China's latest patents, Technical Efficacy Thesaurus, Application Domain, Technology Topic, Popular Technical Reports.
© 2025 PatSnap. All rights reserved.Legal|Privacy policy|Modern Slavery Act Transparency Statement|Sitemap|About US| Contact US: help@patsnap.com