Microhollow super-fibre heat insulation coatings for building insulation and method of use thereof
A technology for building thermal insulation and thermal insulation coatings, applied in the field of coatings, can solve problems such as poor fire resistance and water resistance, poor fire resistance, poor resistance to seepage, and complicated processes, and achieve super chemical stability, outstanding fire resistance, and advanced technology. Effect
- Summary
- Abstract
- Description
- Claims
- Application Information
AI Technical Summary
Problems solved by technology
Method used
Image
Examples
Embodiment 1
[0036] Type I single-component micro-hollow microfiber building thermal insulation coating raw materials are: aramid fiber 3kg, rock wool fiber 4kg, pearl sand 6kg, expanded perlite 8kg, floating beads 4kg, hard silica powder 3kg, fibrous leeches 3kg of stone powder, 3kg of sepiolite, 20kg of acrylic synthetic resin, 15kg of fluorosilicone synthetic resin, 15kg of water-retaining thickener solution, 0.2kg of defoamer, 0.1kg of anti-mold and bactericide, and 3kg of water; The thermal insulation coating of the paste-like construction material.
[0037] Type II two-component micro-hollow microfiber building thermal insulation coating is: the type I single-component micro-hollow microfiber building thermal insulation coating described in claim 1 is one of the raw materials, and the type I single-component 10wt% white portland cement, 5wt% accelerator and 20wt% water of the weight of the micro-hollow microfiber building thermal insulation coating, mixed and stirred evenly to a past...
Embodiment 2
[0051] Type I single-component micro-hollow microfiber building thermal insulation coating raw materials are: aramid fiber 5kg, rock wool fiber 5kg, pearlescent sand 8kg, expanded perlite 10kg, floating beads 6kg, hard silica powder 4kg, fibrous leeches 5kg of stone powder, 4kg of sepiolite, 25kg of acrylic synthetic resin, 20kg of fluorosilicone synthetic resin, 20kg of water-retaining thickener solution, 0.3kg of defoamer, 0.2kg of anti-mold and bactericide, and 3kg of water; The thermal insulation coating of the paste-like construction material.
[0052] Type II two-component micro-hollow microfiber building thermal insulation coating is: the type I single-component micro-hollow microfiber building thermal insulation coating described in claim 1 is one of the raw materials, and the type I single-component 20wt% white portland cement, 10wt% accelerator and 20wt% water of the weight of the micro-hollow microfiber building thermal insulation coating, mixed and stirred evenly t...
Embodiment 3
[0066] Type I single-component micro-hollow microfiber building thermal insulation coating raw materials are: aramid fiber 3.5kg, rock wool fiber 4.2kg, pearl sand 6.5kg, expanded perlite 8.5kg, floating beads 4.5kg, hard silicon calcium powder 3kg, fibrous vermiculite powder 3kg, sepiolite 3.5kg, acrylic synthetic resin 22kg, fluorosilicon synthetic resin 16kg, water-retaining thickener solution 16kg, defoamer 0.25kg, anti-mildew bactericide 0.15kg, water 3kg; The above raw materials are mixed in proportion to form the thermal insulation coating of the mud paste construction material.
[0067]Type II two-component micro-hollow microfiber building thermal insulation coating is: the type I single-component micro-hollow microfiber building thermal insulation coating described in claim 1 is one of the raw materials, and the type I single-component 13wt% white portland cement, 6wt% accelerator and 10wt% water of the weight of the micro-hollow microfiber building thermal insulation...
PUM
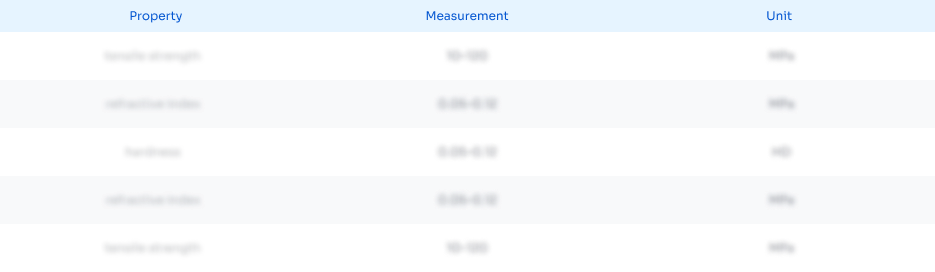
Abstract
Description
Claims
Application Information

- Generate Ideas
- Intellectual Property
- Life Sciences
- Materials
- Tech Scout
- Unparalleled Data Quality
- Higher Quality Content
- 60% Fewer Hallucinations
Browse by: Latest US Patents, China's latest patents, Technical Efficacy Thesaurus, Application Domain, Technology Topic, Popular Technical Reports.
© 2025 PatSnap. All rights reserved.Legal|Privacy policy|Modern Slavery Act Transparency Statement|Sitemap|About US| Contact US: help@patsnap.com