Method and equipment for producing solar array back film
A technology of a solar battery pack and a production method, applied in the field of solar cells, can solve the problems of low production efficiency, unstable performance, high labor intensity, etc., and achieve the effect of reducing the length of the workshop, saving energy consumption, and shortening the length of the box body
- Summary
- Abstract
- Description
- Claims
- Application Information
AI Technical Summary
Problems solved by technology
Method used
Image
Examples
Embodiment 1
[0035] An example of the equipment of the present invention, as shown in Figure 2, includes an unwinding device 1, a pretreatment device 2, a coating device 3, a drying tunnel 4, a finishing device 5, a winding device 6 and a drying device. The unwinding device 1 includes a turning frame type continuous unwinding mechanism and an unwinding traction device; the unwinding shaft set by the unwinding mechanism is a flat key type air expansion shaft; Traction, using magnetic powder brake to control the tension. The pretreatment device 2 includes a static eliminator and a cleaning device. The coating device is a three-roller reverse coating device; the coating thickness is measured and controlled by the comma scraper, the coating speed is controlled by the independent frequency conversion of three motors, and the comma scraper is quickly reset by pneumatics. The length of the drying tunnel is 78m. The drying tunnel is set in the box with the insulation layer. The initial section is...
Embodiment 2
[0037] One example of the method of the present invention is to use the equipment of Example 1 to implement the method of the present invention to produce a single-sided coated solar cell back film. like figure 1 shown, including unwinding, pretreatment, coating, drying, finishing, liner winding and drying steps. First, select tensile strength (N / 10mm) ≥ 110, tear strength (N / mm) 135-145, semi-matt PET film as the base film, place the rolled base film on the unwinding device, and pull The base film is released from the roll; then the base film is electrostatically treated to make its electrostatic induction coefficient ≤0.8, and then cleaned to make the surface of the base film clean and free of impurities; then the imported fluorocarbon paint is stirred evenly and reversed through three rollers The coating device coats the pretreated base film, the coating speed is controlled to be 5m / min, the temperature is 12°C, and the thickness of the coating is controlled by the comma ...
Embodiment 3
[0039]The second example of the method of the present invention is to use the equipment of Example 1 to implement the method of the present invention to produce the back film of a double-sided coated solar cell group. As described in Example 2, through the steps of unwinding, pretreatment, coating, drying, finishing, lining film winding and drying, the single-sided coating was completed. Then separate and rewind the lining film, and process the other side again according to the above process steps, that is, go through the steps of unwinding, pretreatment, coating, drying, finishing, lining film winding and drying again, until the drying is completed again The step is to obtain the finished film. The lining film in the finished film is separated, cut and packaged to obtain the final product.
PUM
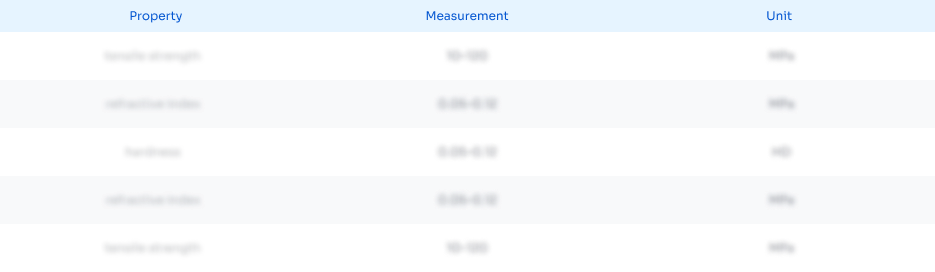
Abstract
Description
Claims
Application Information

- Generate Ideas
- Intellectual Property
- Life Sciences
- Materials
- Tech Scout
- Unparalleled Data Quality
- Higher Quality Content
- 60% Fewer Hallucinations
Browse by: Latest US Patents, China's latest patents, Technical Efficacy Thesaurus, Application Domain, Technology Topic, Popular Technical Reports.
© 2025 PatSnap. All rights reserved.Legal|Privacy policy|Modern Slavery Act Transparency Statement|Sitemap|About US| Contact US: help@patsnap.com