Banana tree paper manufacture technique, slurry storage technique and sewage disposal technique thereof by soft chemistry method
A papermaking process and soft chemistry technology, applied in washing/replacing pulp treatment liquid, pulp dehydration, fiber raw material treatment, etc., can solve problems such as low production efficiency, large loss of raw materials, sewage pollution, etc., and achieve lower production costs and loss of raw materials. Effects of low, significant environmental benefits
- Summary
- Abstract
- Description
- Claims
- Application Information
AI Technical Summary
Problems solved by technology
Method used
Examples
Embodiment 1
[0047] (1) Raw materials: Banana trees, leaves and stems that have been felled for no more than 5 days
[0048] (2), pressing and cutting: put the raw material through a rolling machine to squeeze out 40% of the water and cut it into equal lengths of 1 cm;
[0049](3) Crushing and dispersing: After cutting the material, it is sent to the crusher for crushing through the conveyor belt, and the fibers are detached by high-pressure water to form the primary slurry;
[0050] (4) Sand settling: the initial slurry is desanded through the sand settling ditch;
[0051] (5) Water washing: the initial slurry is sent to the centrifugal tank for water washing after desanding in the sand ditch to remove dirt and mud;
[0052] (6), bleaching: add 0.3% sodium hypochlorite equivalent to dry material weight to the slurry after washing, carry out quick bleaching by heating pipeline;
[0053] (7), pulp refining: add 0.1% sodium linoleate equivalent to dry material weight to the pulp after blea...
Embodiment 2
[0063] (1) Raw materials: Banana trees, leaves and stems that have been felled for no more than 5 days
[0064] (2), pressing and cutting: put the raw material through a rolling machine to squeeze out 60% of the water and cut it into equal lengths of 5 cm;
[0065] (3) Crushing and dispersing: After cutting the material, it is sent to the crusher for crushing through the conveyor belt, and the fibers are detached by high-pressure water to form the primary slurry;
[0066] (4) Sand settling: the initial slurry is desanded through the sand settling ditch;
[0067] (5) Water washing: the initial slurry is sent to the centrifugal tank for water washing after desanding in the sand ditch to remove dirt and mud;
[0068] (6), bleaching: add 10% sodium chlorate equivalent to dry material weight to the slurry after washing, carry out rapid bleaching by heating pipeline;
[0069] (7), refining: add 6% sodium arachidonic acid and potassium linoleate (the mass ratio of the two is 1 to 1...
Embodiment 3
[0079] (1) Raw materials: Banana trees, leaves and stems that have been felled for no more than 5 days
[0080] (2), pressing and cutting: put the raw material through a rolling machine to squeeze out 45% of the water and cut it into equal lengths of 2 cm;
[0081] (3) Crushing and dispersing: After cutting the material, it is sent to the crusher for crushing through the conveyor belt, and the fibers are detached by high-pressure water to form the primary slurry;
[0082] (4) Sand settling: the initial slurry is desanded through the sand settling ditch;
[0083] (5) Water washing: the initial slurry is sent to the centrifugal tank for water washing after desanding in the sand ditch to remove dirt and mud;
[0084] (6), bleaching: add the chlorine dioxide equivalent to 1% of dry material weight to the slurry after washing, carry out quick bleaching by heating pipeline;
[0085] (7), pulp refining: add 1% sodium palmitate equivalent to dry material weight to the pulp after ble...
PUM
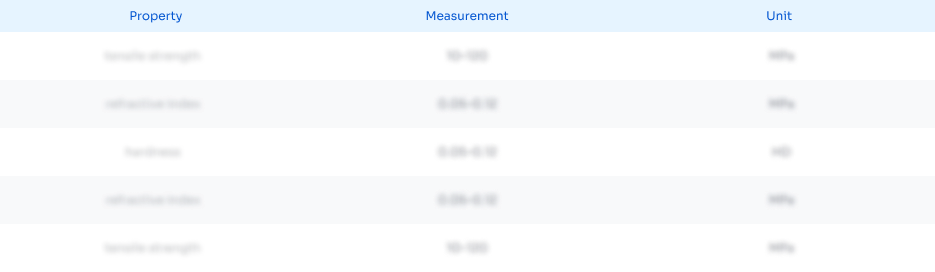
Abstract
Description
Claims
Application Information

- R&D
- Intellectual Property
- Life Sciences
- Materials
- Tech Scout
- Unparalleled Data Quality
- Higher Quality Content
- 60% Fewer Hallucinations
Browse by: Latest US Patents, China's latest patents, Technical Efficacy Thesaurus, Application Domain, Technology Topic, Popular Technical Reports.
© 2025 PatSnap. All rights reserved.Legal|Privacy policy|Modern Slavery Act Transparency Statement|Sitemap|About US| Contact US: help@patsnap.com