Manufacturing method of environment protective paper
A manufacturing method, the technology of environmentally friendly paper, applied in the field of papermaking, can solve the problems that cannot be completely solved, the surface of the product is not uniform, and the production variety is limited, so as to achieve the effect of reducing production cost, good strength and improving quality
- Summary
- Abstract
- Description
- Claims
- Application Information
AI Technical Summary
Problems solved by technology
Method used
Examples
Embodiment 1
[0021] Mineral powder is obtained by grinding dolomite, alabaster, mica, calcite and other stone materials through equipment. Seaweed gel is extracted from natural seaweed. The auxiliary materials include dyeing matter, resin, antistatic agent and lubricant. Firstly, mineral powder and seaweed gel are mixed to form a mixture, the mixture formed by the two raw materials is fused with auxiliary materials to form a mixture of semi-finished raw materials, and the mixture of semi-finished raw materials is extruded, kneaded and granulated to produce Finished raw materials. The ratio of each substance in the raw material of the finished product is 60g of mineral powder, 37g of seaweed gel and 3g of auxiliary material. The finished raw materials are heated at a high temperature in the paper film manufacturing machine to soften the raw materials as a whole, bleaching and related treatments are carried out through auxiliary materials, and the processed raw materials are sent to the pape...
Embodiment 2
[0023] Mineral powder is obtained by grinding dolomite, alabaster, mica, calcite and other stone materials through equipment. Seaweed gel is extracted from natural seaweed. The auxiliary materials include dyeing matter, resin, antistatic agent and lubricant. Firstly, mineral powder and seaweed gel are mixed to form a mixture, the mixture formed by the two raw materials is fused with auxiliary materials to form a mixture of semi-finished raw materials, and the mixture of semi-finished raw materials is extruded, kneaded and granulated to produce Finished raw materials. The ratio of each substance in the raw material of the finished product is 75g of mineral powder, 30g of seaweed gel and 2g of auxiliary material. The finished raw materials are heated at a high temperature in the paper film manufacturing machine to soften the raw materials as a whole, bleaching and related treatments are carried out through auxiliary materials, and the processed raw materials are sent to the pape...
Embodiment 3
[0025] Mineral powder is obtained by grinding dolomite, alabaster, mica, calcite and other stone materials through equipment. Seaweed gel is extracted from natural seaweed. The auxiliary materials include dyeing matter, resin, antistatic agent and lubricant. Firstly, mineral powder and seaweed gel are mixed to form a mixture, the mixture formed by the two raw materials is fused with auxiliary materials to form a mixture of semi-finished raw materials, and the mixture of semi-finished raw materials is extruded, kneaded and granulated to produce Finished raw materials. The ratio of each substance in the raw material of the finished product is 80g of mineral powder, 17g of seaweed gel and 1g of auxiliary material. The finished raw materials are heated at a high temperature in the paper film manufacturing machine to soften the raw materials as a whole, bleaching and related treatments are carried out through auxiliary materials, and the processed raw materials are sent to the pape...
PUM
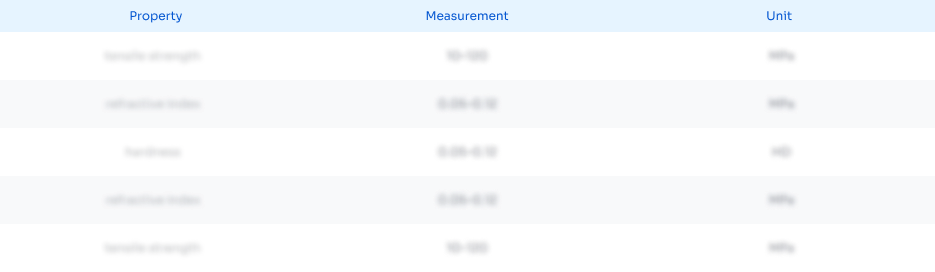
Abstract
Description
Claims
Application Information

- R&D Engineer
- R&D Manager
- IP Professional
- Industry Leading Data Capabilities
- Powerful AI technology
- Patent DNA Extraction
Browse by: Latest US Patents, China's latest patents, Technical Efficacy Thesaurus, Application Domain, Technology Topic, Popular Technical Reports.
© 2024 PatSnap. All rights reserved.Legal|Privacy policy|Modern Slavery Act Transparency Statement|Sitemap|About US| Contact US: help@patsnap.com