Brazing material and preparation method thereof as well as brazing method using the material
A brazing material and brazing technology, applied in the direction of welding/cutting media/materials, welding equipment, manufacturing tools, etc., can solve the problems of high working temperature, connection strength and low working temperature
- Summary
- Abstract
- Description
- Claims
- Application Information
AI Technical Summary
Problems solved by technology
Method used
Image
Examples
Embodiment 1
[0025] (1) According to mass percentage: Cu 45%, Ag 25%, Zn 23%, Ni 5%, Ti 1%, Si1%, weighed as 200 mesh Ag and Cu powder, 300 mesh Zn, Ni, Ti, Si The powder is milled and mixed in a planetary ball mill for 60 minutes, the ball-to-material ratio is 5:1, and the ball mill speed is 200r / min-300r / min to obtain alloy powder. (2) The alloy powder after ball milling is pressed with a powder forming press to obtain a compact with a pressure of 450Mpa; (3) The brazing material compact is sintered in a vacuum, and the sintering temperature is selected at about 750°C and kept for 15 minutes to obtain the thickness The brazing material sheet is about 1 to 3mm; (4) Then annealed and rolled into a brazing material sheet with a thickness of about 0.2mm.
Embodiment 2
[0027] (1) According to the mass percentage: Cu 43%, Ag 23%, Zn 21%, Ni 8%, Ti 2%, Si 3%, weighed to be 200 mesh Ag and Cu powder, 300 mesh Zn, Ni, Ti, The Si powder is ball-milled and mixed in a planetary ball mill for 90 minutes, the ball-to-material ratio is 5:1, and the ball mill speed is 200r / min-300r / min to obtain alloy powder. (2) The alloy powder after ball milling is pressed with a powder forming press to obtain a compact with a pressure of 500Mpa; (3) The brazing material compact is sintered in vacuum, and the sintering temperature is selected at about 780°C, and the temperature is maintained for 20 minutes to obtain the thickness The brazing material sheet is about 1 to 3mm; (4) Then annealed and rolled into a brazing material sheet with a thickness of about 0.2mm.
Embodiment 3
[0029] (1) According to the mass percentage: Cu 40%, Ag 20%, Zn 22%, Ni 10%, Ti 3%, Si 5%, weighed as 200 mesh Ag and Cu powder, 300 mesh Zn, Ni, Ti, The Si powder is ball-milled and mixed in a planetary ball mill for 120 minutes, with a ball-to-material ratio of 5:1, and the speed of the ball mill is 200r / min-300r / min to obtain alloy powder. (2) The alloy powder after ball milling is pressed with a powder forming press to obtain a compact with a pressure of 550Mpa; (3) The sintering of the brazing material compact is vacuum sintering, and the sintering temperature is selected at about 800°C and the temperature is kept for 30 minutes. A brazing material sheet with a thickness of about 1 to 3 mm is obtained; (4) then annealed and rolled into a brazing material sheet with a thickness of about 0.2 mm.
[0030] Brazing method embodiment 1:
[0031] (1) Cut the Ti(C,N)-based cermet and 45 steel into 35mm×8mm×6mm test pieces by wire-cut EDM. Before brazing, the Ti(C,N)-based cermet and ...
PUM
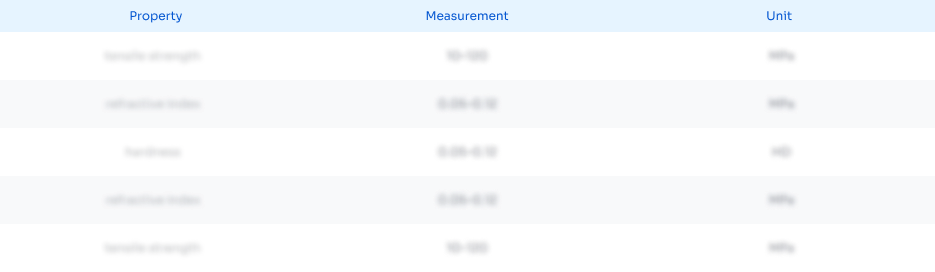
Abstract
Description
Claims
Application Information

- Generate Ideas
- Intellectual Property
- Life Sciences
- Materials
- Tech Scout
- Unparalleled Data Quality
- Higher Quality Content
- 60% Fewer Hallucinations
Browse by: Latest US Patents, China's latest patents, Technical Efficacy Thesaurus, Application Domain, Technology Topic, Popular Technical Reports.
© 2025 PatSnap. All rights reserved.Legal|Privacy policy|Modern Slavery Act Transparency Statement|Sitemap|About US| Contact US: help@patsnap.com