Method for reclaiming cobalt from manganese cobalt slag
A cobalt-nickel, manganese-cobalt technology, applied in the field of hydrometallurgy, can solve the problem of no recovery, etc., and achieve the effects of saving chemical reagent materials, less consumption of chemical reagents, and high recovery rate
- Summary
- Abstract
- Description
- Claims
- Application Information
AI Technical Summary
Problems solved by technology
Method used
Image
Examples
Embodiment Construction
[0019] The technical solutions of the present invention will be described in further detail below through examples.
[0020] The method for reclaiming cobalt-nickel from manganese-cobalt slag of the present invention, concrete operating steps are:
[0021] 1. Add water to mix slurry, heat and bubble
[0022] The purification slag produced in the manganese ore leaching process, referred to as manganese-cobalt slag (the full text is called manganese-cobalt slag), takes 800 grams of this slag (dry weight 544 grams), and the slag contains 5.02 grams of Co, 13.06 grams of Ni, and 32.69 grams of Mn , Fe 30.90 grams. Add water to a 3-liter beaker to dilute to 2200ml, stir and adjust the slurry, while heating and bubbling, and remove the foam slag. The test results are shown in Table 1.
PUM
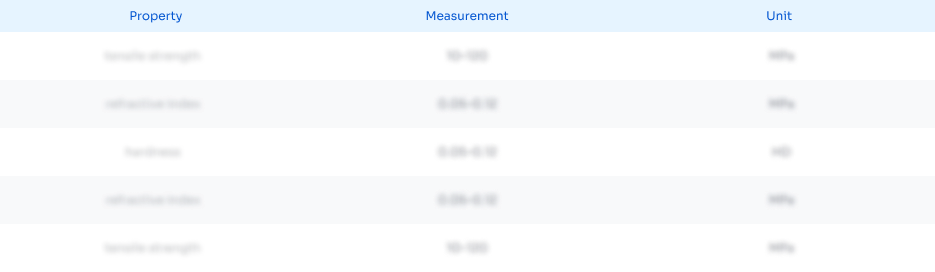
Abstract
Description
Claims
Application Information

- Generate Ideas
- Intellectual Property
- Life Sciences
- Materials
- Tech Scout
- Unparalleled Data Quality
- Higher Quality Content
- 60% Fewer Hallucinations
Browse by: Latest US Patents, China's latest patents, Technical Efficacy Thesaurus, Application Domain, Technology Topic, Popular Technical Reports.
© 2025 PatSnap. All rights reserved.Legal|Privacy policy|Modern Slavery Act Transparency Statement|Sitemap|About US| Contact US: help@patsnap.com