Black master batch for AS system plastic and preparation method thereof
A technology of black masterbatch and plastic, applied in the field of color masterbatch of copolymer and its preparation, can solve the problems of blackness and glossiness, difficulty in uniformity of color difference and glossiness, and difficulty in dispersing carbon black, and achieve glossiness. High efficiency, improve equipment efficiency, and reduce the effect of processing equipment requirements
- Summary
- Abstract
- Description
- Claims
- Application Information
AI Technical Summary
Problems solved by technology
Method used
Examples
Embodiment 1
[0013] Formula: AS plastic: 75.8wt%, acetyl tributyl citrate: 0.8wt%, ethylene bisstearamide: 2.4wt%, mixed dye: 21wt%.
[0014] The mixed dye composition is: oil soluble blue B 35#: 30wt%, solvent yellow 14#: 50wt%, transparent green 5B3#: 5wt%, disperse violet 28#: 5wt%, solvent red 24#: 10wt%.
[0015] Preparation method: set the temperature of the mixing room of the internal mixer to 170°C, and after the temperature reaches the set temperature, put a total amount of 57wt% AS plastic into the internal mixer, then add acetyl tributyl citrate, and internally mix for 30 Minutes, put ethylene bis stearic acid amide into the banburying kettle, continue banburying for 5 minutes, put the mixed dye 1 into the banburying kettle, continue kneading with the banburying machine for 30 minutes, unload and cool to room temperature naturally, and grind The equipment crushes the material, then mixes it with the remaining 43wt% of AS plastic, extrudes and granulates it through a twin-screw e...
Embodiment 2
[0017] Formula: AS1: 91.75wt%, acetyl tributyl citrate: 0.75wt%, ethylene bis stearic acid amide: 2.5wt%, mixed dye: 5wt%. Mixed dye composition is identical with embodiment 1.
[0018] Preparation method: set the temperature of the mixing chamber of the internal mixer to 170°C, and after the temperature reaches the set temperature, put a total amount of 58wt% AS plastic into the internal mixer, then add acetyl tributyl citrate, and internally mix for 30 Minutes, put ethylene bis stearic acid amide into the banburying kettle, continue banburying for 5 minutes, put the mixed dye 1 into the banburying kettle, continue kneading with the banburying machine for 30 minutes, unload and cool to room temperature naturally, and grind The equipment pulverizes the material, then mixes it with the remaining 42wt% of AS plastic, extrudes and granulates through a twin-screw extruder to obtain AS black masterbatch.
PUM
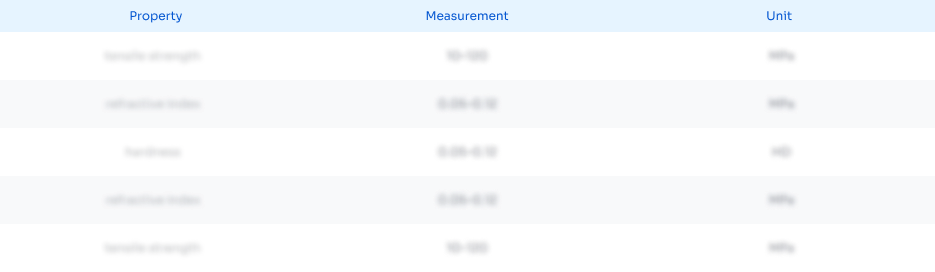
Abstract
Description
Claims
Application Information

- Generate Ideas
- Intellectual Property
- Life Sciences
- Materials
- Tech Scout
- Unparalleled Data Quality
- Higher Quality Content
- 60% Fewer Hallucinations
Browse by: Latest US Patents, China's latest patents, Technical Efficacy Thesaurus, Application Domain, Technology Topic, Popular Technical Reports.
© 2025 PatSnap. All rights reserved.Legal|Privacy policy|Modern Slavery Act Transparency Statement|Sitemap|About US| Contact US: help@patsnap.com