Gasification process of water/gas mixed partial-chilled dry powder fuel and device
A fuel gasification and mixing technology, which is applied in the gasification of granular/powder fuel, petroleum industry, and the manufacture of combustible gas, etc. It can solve the problems of difficulty in uniform mixing, insufficient steam content, and long manufacturing cycle, etc., to achieve increased flow rate, Strengthen the cooling effect and reduce the metal wall temperature
- Summary
- Abstract
- Description
- Claims
- Application Information
AI Technical Summary
Problems solved by technology
Method used
Image
Examples
Embodiment Construction
[0027] Below in conjunction with accompanying drawing, the present invention will be further explained:
[0028] Referring to Fig. 1, the process method of the present invention is as follows: dry coal powder is mixed with oxygen and part of the steam and enters the furnace of the gasification furnace 10 through the burner on the gasification furnace 10, and reacts in the furnace to generate high-temperature crude syngas at a temperature of about 1400-1700°C, the gasification pressure in the furnace is 0-8.0MPa, the crude synthesis gas flows from bottom to top after being collided and mixed in the gasifier 10, and the middle and / or upper part of the gasifier 10 is surrounded by two ring-shaped Part of the water / gas mixed mist sprayed by the phase flow atomization jet cooling device 9 (in this embodiment, the water / gas mixed mist is a mist mixed with water and steam) is partially cooled to 400-500°C, The cooled crude syngas passes through the cyclone dust collector 11 to remove...
PUM
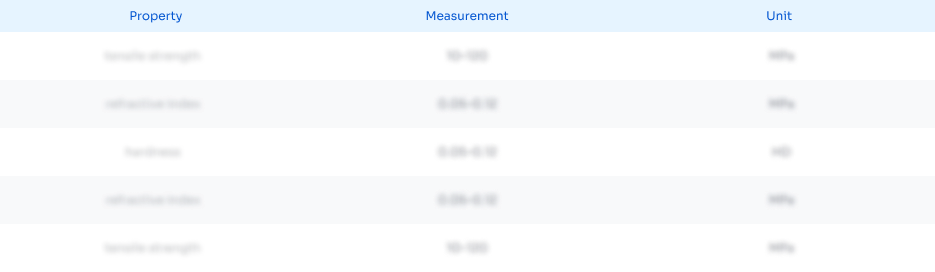
Abstract
Description
Claims
Application Information

- R&D Engineer
- R&D Manager
- IP Professional
- Industry Leading Data Capabilities
- Powerful AI technology
- Patent DNA Extraction
Browse by: Latest US Patents, China's latest patents, Technical Efficacy Thesaurus, Application Domain, Technology Topic, Popular Technical Reports.
© 2024 PatSnap. All rights reserved.Legal|Privacy policy|Modern Slavery Act Transparency Statement|Sitemap|About US| Contact US: help@patsnap.com