Method for manufacturing silicon carbide nanometer fibre/carbon fibre composite felt body
A nanofiber and composite felt technology is applied in the field of felt body preparation to achieve the effects of convenient operation, simple equipment and easy control
- Summary
- Abstract
- Description
- Claims
- Application Information
AI Technical Summary
Problems solved by technology
Method used
Image
Examples
Embodiment 1
[0017] Soak the needle-punched whole carbon felt with acetone for 24 hours, repeatedly soak and clean it with deionized water, and after drying, use this sample as the cathode, nickel sulfate solution as the electroplating solution (concentration is 200g / L), pH value is 5, in When the current intensity is 80mA, electroplating for 5 minutes, soaking in deionized water, cleaning, and drying at a temperature of 100°C for 6 hours, deposit silicon carbide in a chemical vapor deposition furnace, and control the deposition gas source Trichloromethylsilane (MTS) , carrier gas hydrogen (H 2 ) and dilute argon (Ar) at a flow ratio of about 1:3:4, the deposition temperature is 1273K, the furnace pressure is 30Pa, the deposition time is 2 hours, and the furnace is cooled with the furnace. The needle-punched integral carbon felt after electroplating nickel and chemical vapor deposition was taken for SEM microscopic appearance observation, the accelerating voltage was 30KV, and the microsco...
Embodiment 2
[0019] Soak the whole needle-punched carbon felt with acetone for 24 hours, repeatedly soak and clean it with deionized water, and after drying, use this sample as the cathode, cobalt sulfate solution (concentration is 160g / L) as the electroplating solution, and the pH value is 3. When the current intensity is 120mA, electroplating for 10 minutes, soaking in deionized water, cleaning, and drying at a temperature of 120°C for 2 hours, deposit silicon carbide in a chemical vapor deposition furnace, and control the deposition gas source Trichloromethylsilane (MTS) , carrier gas hydrogen (H 2 ) and dilute argon (Ar) at a flow ratio of about 1:2:3, the deposition temperature is 1373K, the furnace pressure is 20Pa, the deposition time is 1 hour, and it is released after cooling with the furnace.
Embodiment 3
[0021] The needle-punched whole carbon felt was repeatedly soaked and cleaned with deionized water (that is, without degumming), and after drying, it was washed with SnCl 2 (15g / L) and hydrochloric acid (30ml / L) mixture as a sensitizer, sensitized at room temperature for 2 minutes, soaked in deionized water repeatedly and washed in PdCl 2 (0.4g / L) and hydrochloric acid (8ml / L) mixed solution for activation for 6 minutes, after repeated immersion and cleaning in deionized water, in CoSO 4 (8~12g / L), NaH 2 PO 2 (23g / L), NaC 2 h 3 o 2 (20g / L), Na 3 C 6 h 5 o 7 (25g / L) and PdNO 3 (6mg / L) mixed solution, controlled temperature is 80 ℃, pH value is 4 when electroless plating 2 minutes, deionized water soaking, cleaning, after drying at 110 ℃ for 4 hours, deposited in chemical vapor deposition furnace Silicon carbide, controlled deposition gas source trichloromethylsilane (MTS), carrier gas hydrogen (H 2 ) and dilute argon (Ar) at a flow ratio of 1:2:4, the deposition temp...
PUM
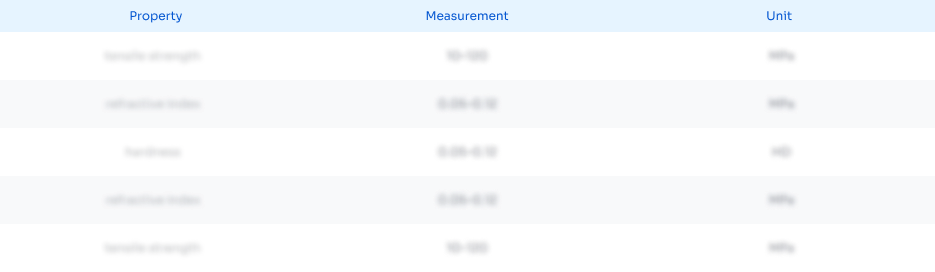
Abstract
Description
Claims
Application Information

- R&D
- Intellectual Property
- Life Sciences
- Materials
- Tech Scout
- Unparalleled Data Quality
- Higher Quality Content
- 60% Fewer Hallucinations
Browse by: Latest US Patents, China's latest patents, Technical Efficacy Thesaurus, Application Domain, Technology Topic, Popular Technical Reports.
© 2025 PatSnap. All rights reserved.Legal|Privacy policy|Modern Slavery Act Transparency Statement|Sitemap|About US| Contact US: help@patsnap.com