A making method for anode slice of lithium ion battery
A technology for lithium ion batteries and positive electrode pieces, which is applied in electrode manufacturing, battery electrodes, active material electrodes, etc., can solve the problems of reducing the processing performance of positive electrode pieces, reducing the content of active material, and increasing the difficulty of battery control, so as to improve the capacity. and cycle performance, improve compaction density, and are not easy to crack.
- Summary
- Abstract
- Description
- Claims
- Application Information
AI Technical Summary
Problems solved by technology
Method used
Examples
preparation example Construction
[0015] The method for preparing the positive pole piece of the lithium ion battery of the present invention is suitable for the commonly used positive electrode materials in this field. For example, lithium cobalt oxide, lithium manganate, lithium nickel cobalt oxide series binary materials, and nickel cobalt manganese series ternary materials can be selected. , At least one of phosphate series cathode materials (such as lithium iron phosphate, lithium vanadium phosphate, etc.), lithium titanate or lithium vanadate.
[0016] In the method for preparing the positive pole piece of the lithium ion battery of the present invention, the addition time of the binder during the homogenization process can be selected by adding two or more binders with different molecular weights to the solvent simultaneously or randomly step by step In the process of dissolving the glue, you can also directly add the above-mentioned binder to the positive active material and the conductive agent powder at ...
Embodiment 1
[0020] In the homogenization of the lithium iron phosphate positive electrode slurry, two polyvinylidene fluorides with molecular weights of 350,000 and 700,000 were selected as binders, referred to as binders A and B, and NMP as the solvent. The mass ratios of the two kinds of polyvinylidene fluoride binders with different molecular weights are 10:0, 7:3, 5:5, 3:7, 2:8, 1:9 and 0:10, respectively. The agent is added to the solvent at the same time, stirred to dissolve the glue, mixed with the powder to homogenize, and coated on the current collector to prepare the positive pole piece. The bonding strength and maximum compaction density of the pole pieces obtained by testing the above ratio are shown in Table 1.
[0021] It can be seen that when the mass ratio of the low-molecular-weight adhesive A in the total amount of the adhesive does not exceed 50%, the bonding effect and processability of the pole piece are better, especially the low-molecular-weight adhesive A and the high-...
Embodiment 2
[0026] The two binders in Example 1 were added at the same time. Instead, the high molecular weight binder B was added and stirred for 15 minutes, and then the low molecular weight binder B was added and mixed and stirred to make the glue. The remaining steps are the same as in Example 1. The results of the measured bond strength and compaction density are shown in Table 2. The results show that adding binders of different molecular weights to the solvent to dissolve the glue at the same time or step by step has little effect on the bonding effect and processability of the pole piece.
[0027] Table 2 Add two different molecular weight polyvinylidene fluoride binders in different periods
[0028] Test result when making glue homogenate
[0029] A: B
PUM
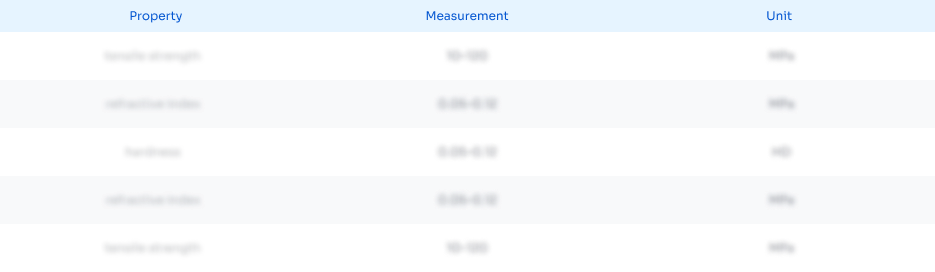
Abstract
Description
Claims
Application Information

- R&D
- Intellectual Property
- Life Sciences
- Materials
- Tech Scout
- Unparalleled Data Quality
- Higher Quality Content
- 60% Fewer Hallucinations
Browse by: Latest US Patents, China's latest patents, Technical Efficacy Thesaurus, Application Domain, Technology Topic, Popular Technical Reports.
© 2025 PatSnap. All rights reserved.Legal|Privacy policy|Modern Slavery Act Transparency Statement|Sitemap|About US| Contact US: help@patsnap.com