High-temperature wearable composite dope for electric power boiler flue
A high-temperature wear-resistant, composite coating technology, used in coatings, combustion product treatment, exhaust gas devices, etc., can solve the problem of high-temperature volume stability, erosion resistance and wear resistance, and acid gas corrosion resistance Reduce, liner deformation and wear resistance and other issues, to achieve the effect of improving high temperature volume stability and wear resistance, reducing the number of repairs and maintenance, and improving high temperature performance
- Summary
- Abstract
- Description
- Claims
- Application Information
AI Technical Summary
Problems solved by technology
Method used
Examples
Embodiment 1
[0032] The high-temperature wear-resistant composite coating for electric boiler flue of the present invention contains the following components and contents calculated by mass percentage:
[0033] The granular raw material is super high bauxite, the particle size is 5-3mm, and the addition amount is 15%.
[0034] The raw material of the particles is sub-white corundum, the particle size is 3-1mm, the addition amount is 30%, and the particle size is 1-0mm, the addition amount is 20%.
[0035] The addition amount of white corundum fine powder with a particle size of 200 mesh is 3.0%
[0036] Bimodal α-Al 2 o 3 Micro-powder and nano-silica micro-powder are compounded, and the addition amount is 10%;
[0037] Reinforced particle material is boron carbide CB 4 The addition amount is 5%;
[0038] The binder is hydrated alumina p-Al 2 o 3 The addition amount is 4%;
[0039] The admixture is FDN and sodium hexametaphosphate, and the addition amount is 1.0%;
[0040] The addi...
Embodiment approach 2
[0051] The high-temperature wear-resistant composite coating for electric boiler flue of the present invention contains the following components and contents calculated by mass percentage:
[0052] Granular raw materials are two composites of brown corundum and tabular corundum, with a particle size of 5-3mm, adding 20%; for a particle size of 3-1mm, adding 30%; for a particle size of 1-0mm, adding 20% white corundum fine powder 320 Adding amount is 2.0%
[0053] Chromium Oxide Cr 2 o 3 Micropowder, two composites of silicon carbide SiC micropowder, the addition amount is 7%;
[0054] The reinforcing particle material is titanium boride TiB 2 , zirconium boride ZrB 2 The two kinds of composites, the addition amount is 3%;
[0055] The binder is Lafarge cement Secar71 and the addition of pure calcium aluminate cement is 6%;
[0056] The admixture is two kinds of compound (addition) of sodium tartrate and sodium pyrophosphate, and the addition amount is 0.25%;
[0057] ...
Embodiment approach 3
[0062] The high-temperature wear-resistant composite coating for electric boiler flue of the present invention contains the following components and contents calculated by mass percentage:
[0063] The granular raw material is three composites of super-grade high-bauxite, sintered mullite, and sub-white corundum. The dosage is 20% for particle size 5-3mm, 32% for particle size 3-1mm, and 16% for particle size <1.0mm. %;
[0064] The powder is chromium oxide Cr 2 o 3 Micropowder, silicon carbide SiC micropowder, and multimodal alumina micropowder are compounded of three kinds, the addition amount is 15%;
[0065] Reinforced particle material is boron carbide CB 4 , silicon nitride Si 3 N 4 1. Three kinds of composites of silicon carbide SiC hard particles, the addition amount is 2.0%;
[0066] The binder is Lafarge cement Secar71, pure calcium aluminate cement, and bauxite cement, and the addition amount is 8%;
[0067] The admixture is three compounds of sodium hexameta...
PUM
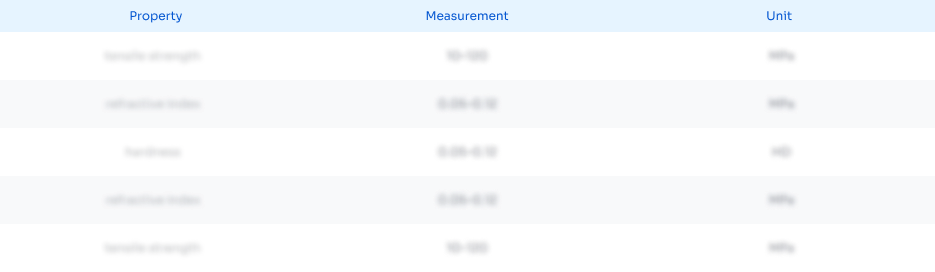
Abstract
Description
Claims
Application Information

- R&D
- Intellectual Property
- Life Sciences
- Materials
- Tech Scout
- Unparalleled Data Quality
- Higher Quality Content
- 60% Fewer Hallucinations
Browse by: Latest US Patents, China's latest patents, Technical Efficacy Thesaurus, Application Domain, Technology Topic, Popular Technical Reports.
© 2025 PatSnap. All rights reserved.Legal|Privacy policy|Modern Slavery Act Transparency Statement|Sitemap|About US| Contact US: help@patsnap.com