Chlorination aromatic hydrocarbon waste gases catalytic purification method
A catalytic purification and exhaust gas technology, applied in chemical instruments and methods, separation methods, and dispersed particle separation, etc., can solve the problems of easy loss of active components of catalysts, low catalytic combustion activity, short catalyst life, etc., and achieve environmental protection applications Prospect, effect of low catalyst cost
- Summary
- Abstract
- Description
- Claims
- Application Information
AI Technical Summary
Problems solved by technology
Method used
Examples
Embodiment 1
[0029] Take 3.0g of cetyltrimethylammonium bromide (CTMAB) and add 105ml of deionized water to dissolve at 30°C to produce a transparent template solution; then add 35ml of ethylenediamine (EDA) under stirring Put it into the flask together with the template solution and keep it at 30°C; then slowly drop the mixed solution of 15ml tetraethyl orthosilicate (TEOS) and 50ml deionized water into the above-mentioned system containing template agent, ethylenediamine and water, So that the amount of each substance in the system satisfies: n(TEOS):n(CTMAB):n(EDA):n(H 2 (0)=1: 0.12: 9.7: 130, stirred for 15min, and the pH of the acetic acid regulator system was 10.5, and after continuing to stir for 1.5h, the sol mixture was transferred to a 100ml stainless steel reactor with a polytetrafluoroethylene liner, at 120 It was statically crystallized in an oven at ℃ for 72 hours under its own pressure, taken out and cooled, washed with deionized water, filtered with suction, washed with abs...
Embodiment 2
[0036] Prepare cerium nitrate and copper nitrate into 0.923M and 0.89M aqueous solutions, adjust the pH value of the salt solution to 5 with ammonia water, take 14mL, and make MCM-41 / PO with various phosphoric acid contents according to the method of Example 1 3 10%CuO-20%CeO supported by H carrier 2 Catalyst 10g. Weigh 100mg of the catalyst, the reaction temperature is 350°C, the moisture content in humid air is 0.2vol%, the concentration of chlorobenzene is 0.1vol%, and the molar ratio of water to chlorobenzene is 2:1; The amount of waste gas is 30L, and the reaction pressure is 0.1Mpa. All the other reaction conditions are the same as in Example 1, the conversion rate of chlorobenzene is shown in Table 2, and the reaction products are carbon dioxide, hydrogen chloride and a trace amount of chlorine.
[0037] Table 2 10%MnOx-20%CeO supported on MCM-41 supports with different Si / P ratios 2 Chlorobenzene conversion rate (350°C)
[0038] Si / P(atom)
Embodiment 3
[0040] Commercially available SiO 2 Surface area is 303m 2 / g, by impregnating phosphoric acid in Example 1, SiO with various phosphoric acid contents 2 / PO 3 H carrier. Prepare aqueous solutions with concentrations of lanthanum nitrate, cerium nitrate, and manganese nitrate of 0.438M, 0.41M, and 0.82M respectively, adjust the pH value of the salt solution to 5 with ammonia water, take 14mL, and impregnate it on various carriers. The method of embodiment 1 is carried out, obtains 10La 2 o 3 -10%CeO 2 -10%MnOx / SiO 2 / PO 3 H catalyst. Weigh 200mg of each catalyst of this series, the reaction temperature is 350°C, the reaction pressure is 0.5Mpa, the moisture content in the humid air is 0.15vpl%, the concentration of chlorobenzene is 0.05vol%, and the amount of waste gas treated per gram of catalyst per hour is 15L, all the other reaction conditions are the same as in Example 1, the conversion rate of chlorobenzene is shown in Table 3, and the reaction products are carbo...
PUM
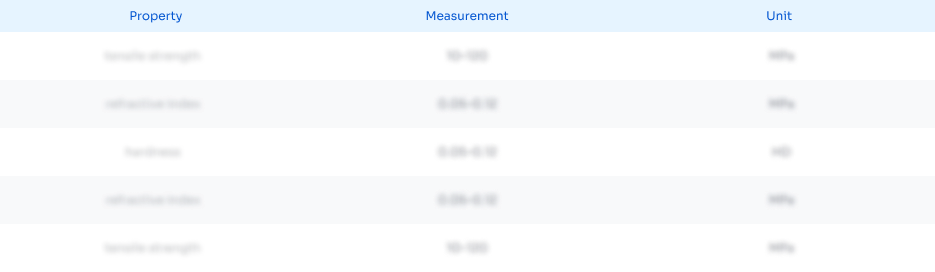
Abstract
Description
Claims
Application Information

- R&D
- Intellectual Property
- Life Sciences
- Materials
- Tech Scout
- Unparalleled Data Quality
- Higher Quality Content
- 60% Fewer Hallucinations
Browse by: Latest US Patents, China's latest patents, Technical Efficacy Thesaurus, Application Domain, Technology Topic, Popular Technical Reports.
© 2025 PatSnap. All rights reserved.Legal|Privacy policy|Modern Slavery Act Transparency Statement|Sitemap|About US| Contact US: help@patsnap.com