Method for preparing straw pulp with high yield by oxidation kneading and equipment used therefor
A high-yield, straw technology, applied in the direction of pretreatment with oxygen-generating compounds, finely split raw material pretreatment, digesters, etc., can solve the problems of low pulp yield, environmental pollution, difficult water treatment, etc. Scientific and reasonable, guarantee the effect of strength
- Summary
- Abstract
- Description
- Claims
- Application Information
AI Technical Summary
Problems solved by technology
Method used
Image
Examples
Embodiment 1
[0017] As shown in Fig. 1, firstly, the straw is cut off and dust-removed, and then input into the feed port 2 of the oxygen soaker 1 . The various components of agricultural straw are composed of cellulose, hemicellulose, lignin and miscellaneous cells. Its characteristics are due to the short growth period of straw, loose mesh structure, poor compactness, and lignin is easily oxidized. Then prepare the auxiliaries. The auxiliary agent is formed by mixing the following components according to weight percentage: 4% sodium hydroxide, 5% hydrogen peroxide, 2% sodium silicate, 0.01% magnesium sulfate, and 0.3% grafted starch. Then dilute the prepared auxiliary agent with water, heat it to 70°C, spray it into the material, stir the auxiliary agent and the material evenly, and input it into the oxygen soaker 1. A large number of conveyor belts 3 arranged horizontally are arranged in the oxygen soaker 1 , and the conveyor belts 3 are driven by power rollers 4 to move circularly. ...
Embodiment 2
[0021] A method for processing high-yield straw pulp by an oxidation kneading machine, which includes the following processing steps: first, cutting the straw and feeding it into an oxygen soaker 1 for oxygen soaking; second, preparing an oxygen soaking auxiliary agent, which contains 3% sodium hydroxide, 3% hydrogen peroxide, 3% sodium silicate, 0.005% magnesium sulfate and 0.1% grafted starch; thirdly, after diluting the prepared additives with water, dilute the prepared When the above-mentioned auxiliary agent is heated to 60°C, it is sprayed into the material, and then the above-mentioned auxiliary agent and the material are stirred evenly and then input into the oxygen soaker 1 for reaction; fourthly, the material after oxygen soaking is input into the rubbing machine 8 for longitudinal separation into filaments ; The fifth, after kneading, the material is input into the oxygen decomposer 10 for oxygen decomposition.
[0022] The reaction temperature in the oxygen soaker ...
Embodiment 3
[0026] A method for processing high-yield straw pulp by an oxidation kneading machine, which includes the following processing steps: first, cutting the straw and feeding it into an oxygen soaker 1 for oxygen soaking; second, preparing an oxygen soaking auxiliary agent, which contains 5% sodium hydroxide, 6% hydrogen peroxide, 5% sodium silicate, 0.015% magnesium sulfate and 0.5% grafted starch; thirdly, after diluting the prepared auxiliary agent with water, dilute the prepared When the additives are heated to 80°C, they are sprayed into the materials, and then the additives and the materials are stirred evenly and then input into the oxygen immersion device 1 for reaction; fourth, the materials after oxygen immersion are input into the kneading machine 8 for longitudinal separation into filaments ; The fifth, after kneading, the material is input into the oxygen decomposer 10 for oxygen decomposition.
[0027] The reaction temperature in the oxygen soaker 1 is 80° C., and th...
PUM
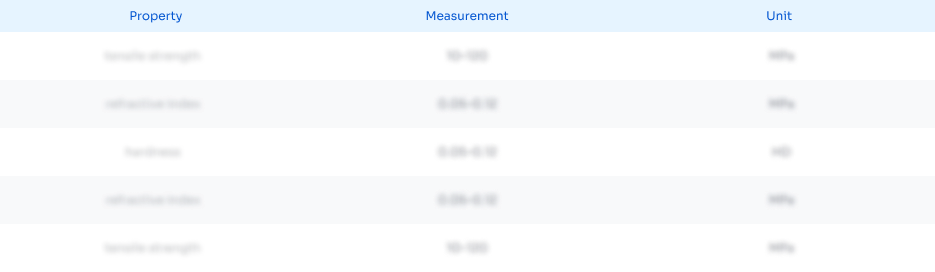
Abstract
Description
Claims
Application Information

- R&D
- Intellectual Property
- Life Sciences
- Materials
- Tech Scout
- Unparalleled Data Quality
- Higher Quality Content
- 60% Fewer Hallucinations
Browse by: Latest US Patents, China's latest patents, Technical Efficacy Thesaurus, Application Domain, Technology Topic, Popular Technical Reports.
© 2025 PatSnap. All rights reserved.Legal|Privacy policy|Modern Slavery Act Transparency Statement|Sitemap|About US| Contact US: help@patsnap.com