High-speed plastic-injecting dump energy pressure maintaining injection molding of plastic method
An injection molding and energy storage technology, applied in the field of injection molding technology, can solve the problems of high energy consumption and slow response time, and achieve the effect of small machine size, fast production cycle and simple mechanical structure
- Summary
- Abstract
- Description
- Claims
- Application Information
AI Technical Summary
Problems solved by technology
Method used
Image
Examples
Embodiment Construction
[0022] In order to further understand the features, technical means, and achieved specific objectives and functions of the present invention, the present invention will be further described in detail below in conjunction with structural schematic diagrams and specific implementation methods.
[0023] The related structure of the present invention mainly includes the following parts (or devices): fixed mold 1, movable mold 2, barrel assembly 3, plasticizing screw 4, injection cylinder assembly 5, energy storage injection generating device 6, energy storage pressure maintaining Generating device 7, oil return control device 8.
[0024] The high-speed injection molding method of the present invention is a molding method of quickly dumping energy and maintaining pressure after high-speed injection is completed, and the process route is as follows:
[0025] ①. Firstly, the energy storage injection generator 6 of the injection energy storage tank stores energy, and at the same time,...
PUM
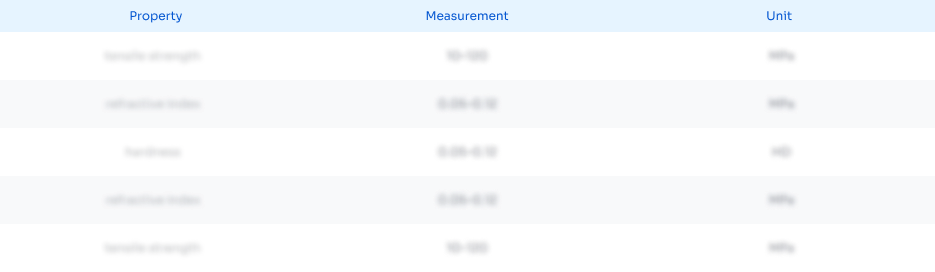
Abstract
Description
Claims
Application Information

- R&D
- Intellectual Property
- Life Sciences
- Materials
- Tech Scout
- Unparalleled Data Quality
- Higher Quality Content
- 60% Fewer Hallucinations
Browse by: Latest US Patents, China's latest patents, Technical Efficacy Thesaurus, Application Domain, Technology Topic, Popular Technical Reports.
© 2025 PatSnap. All rights reserved.Legal|Privacy policy|Modern Slavery Act Transparency Statement|Sitemap|About US| Contact US: help@patsnap.com