Metal removing solution and metal removing method using the same
A metal, palladium alloy technology, applied in the field of metal removal liquid, can solve the problems of tin hydroxide precipitation, copper corrosion and other problems
- Summary
- Abstract
- Description
- Claims
- Application Information
AI Technical Summary
Problems solved by technology
Method used
Image
Examples
Embodiment 1~7、 comparative example 1~3
[0055] 1. Palladium removal test
[0056] Manufacturing method of Pd attachment plate
[0057] A substrate made of glass epoxy resin with a thickness of 0.2 mm, a length of 10 cm, and a width of 10 cm was processed as follows to produce a Pd adhesion plate.
[0058] (1) Dip in a pretreatment solution (PIW-1 manufactured by Okuno Pharmaceutical Co., Ltd.) at 45°C for 2 minutes, wash with water, and dip in ATS CONDICLEAN solution (CIW-1 manufactured by Okuno Pharmaceutical Co., Ltd.) at 65°C for 5 minutes. Minutes to roughen the resin substrate.
[0059] (2) Neutralization was carried out by dipping in a pre-soak solution (OPC-SALH manufactured by Okuno Pharmaceutical Co., Ltd.) at 25° C. for 2 minutes.
[0060] (3) Use a catalyst (OPC-SALH manufactured by Okuno Pharmaceutical Co., Ltd., OPC-80 manufactured by the company) at 25°C for 15 minutes, wash with water, and use an accelerator (OPC-505A manufactured by Okuno Pharmaceutical Co., Ltd., OPC-80 manufactured by the company...
Embodiment 8
[0061] (Example 8, Comparative Example 4)
[0062] The glass epoxy resin substrates of Examples 1 to 7 and Comparative Examples 1 to 3 above were replaced with copper plates (manufactured by Hitachi Chemical Co., Ltd., trade name "MCL-E-679", thickness 0.2 mm) and fabricated on copper substrates. The Pd adhesion plate to which palladium was adhered was used as Example 8 and Comparative Example 4.
[0063] The resulting Pd adhesion plate was immersed in the solution formed by the ingredients shown in Tables 1 to 3 (the remainder is ion-exchanged water) and under the conditions of temperature and time, and then the residual Pd was measured. The removal rate is shown in the table 1 to 3.
[0064] [Table 1]
[0065] Complex
untreated substrate
Example 1
Example 2
Example 3
Example 4
chain thiocarbonyl
base compound
DMTU
50wt%
DMTU
0.05wt%
DMTU
6wt%
7wt%
NaCl
10wt%
...
Embodiment 9
[0076] In this example, a copper corrosion rate test was performed. With the compounding liquid of above-mentioned embodiment 6 and the compounding liquid of comparative example 4, promptly the hydrochloric acid of 35% by weight is 8% by weight, the nitric acid of 65% by weight is 20% by weight, and the remainder is the solution that ion-exchange water mixes to compare copper corrosion rate.
[0077] A copper plate (manufactured by Hitachi Chemical Industry Co., Ltd., trade name MCL-E-679, thickness: 0.2 mm, length: 4 mm, width: 4 mm) was immersed in 100 ml of each solution for 1 minute, and the corrosion rate was measured based on the weight change of the copper plate. The results of measuring the corrosion rate for each copper concentration are shown in FIG. 1 . The reason why the corrosion rate at each copper concentration was measured is because the copper concentration in the solution increases and the copper corrosion rate increases when the substrate is continuously pr...
PUM
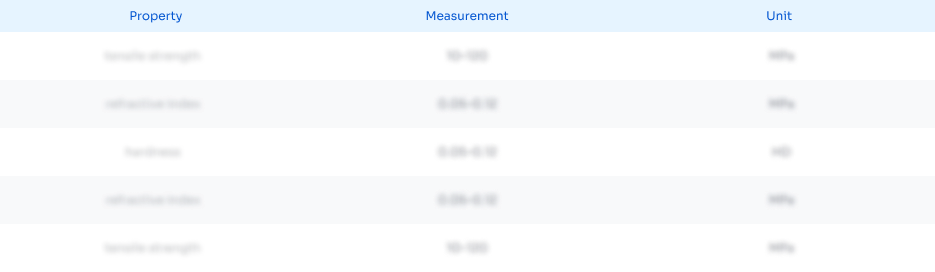
Abstract
Description
Claims
Application Information

- R&D
- Intellectual Property
- Life Sciences
- Materials
- Tech Scout
- Unparalleled Data Quality
- Higher Quality Content
- 60% Fewer Hallucinations
Browse by: Latest US Patents, China's latest patents, Technical Efficacy Thesaurus, Application Domain, Technology Topic, Popular Technical Reports.
© 2025 PatSnap. All rights reserved.Legal|Privacy policy|Modern Slavery Act Transparency Statement|Sitemap|About US| Contact US: help@patsnap.com