Method for preparing polylactic acid group block copolymer
A block copolymer and polylactic acid-based technology, which is applied in the field of preparation of polylactic acid-based block copolymers, can solve the problems of limited wide application, high production cost, insufficient polylactic acid toughness, etc., and achieves simple process and easy industrial production. Effect
- Summary
- Abstract
- Description
- Claims
- Application Information
AI Technical Summary
Problems solved by technology
Method used
Examples
Embodiment 1
[0022] (1) 400g of L-lactic acid and 1,4-butanediol carbonate (molecular weight 2000) 20g are joined in the vacuum reactor, add catalyzer stannous octoate 0.5%, vacuumize, the pressure in the reactor is 1500Pa, The temperature is 100°C, react for 2 hours, then reduce the pressure in the reactor to below 100Pa, raise the reaction temperature to 160°C, and continue the reaction for 16h to obtain M w =0.8×10 3 ~3.0×10 4 Lactic acid prepolymer;
[0023] (2) The lactic acid prepolymer obtained in the step (1) is added in the reactor, vacuumized, logical N 2 Gas, add chain extender hexamethylene diisocyanate (HDI) and catalyzer tin protochloride, carry out chain extension reaction, wherein PLA and HDI molar ratio are 3: 1, stannous octoate add-on is 1%; Reaction temperature At 170°C, react for 30 minutes to obtain the desired product, the product weight average molecular weight M w 1×10 5 ~2×10 5 .
Embodiment 2
[0025] (1) 800g of L-lactic acid and 1,4-butanediol polycarbonate (molecular weight 3000) 40g are added in the vacuum reactor, add catalyst stannous chloride 0.7%, vacuumize, the pressure in the reactor is 1000Pa , the temperature was 120°C, reacted for 5 hours, then lowered the pressure in the reactor to below 100Pa, raised the reaction temperature to 200°C, and continued to react for 15 hours to obtain M w =0.8×10 3 ~3.0×10 4 Lactic acid prepolymer;
[0026] (2) The lactic acid prepolymer obtained in the step (1) is added in the reactor, vacuumized, logical N 2 gas, add chain extender hexamethylene diisocyanate (HDI) and catalyst triethylenediamine, carry out chain extension reaction, wherein the molar ratio of PLA and HDI is 2: 1, and the addition of triethylenediamine is 0.5% ; Reaction temperature is 150 ℃, reacts for 50 minutes, promptly obtains desired product, and this product weight-average molecular weight M w 1×10 5 ~2×10 5 .
Embodiment 3
[0028] (1) 800g of L-lactic acid and 1,6-hexanediol polycarbonate (molecular weight 4000) 40g are added in the vacuum reactor, add catalyst stannous bromide 1%, vacuumize, the pressure in the reactor is 1800Pa , the temperature was 110°C, reacted for 3 hours, then lowered the pressure in the reactor to below 100Pa, raised the reaction temperature to 150°C, and continued to react for 20 hours to obtain M w =0.8×10 3 ~3.0×10 4 Lactic acid prepolymer;
[0029] (2) The lactic acid prepolymer obtained in the step (1) is added in the reactor, vacuumized, logical N 2 Gas, add chain extender hexamethylene diisocyanate (HDI) and catalyzer dibutyltin dilaurate, carry out chain extension reaction, wherein PLA and HDI molar ratio are 2.5: 1, dibutyltin dilaurate add-on is 2%; the reaction temperature is 160°C, and after 20 minutes of reaction, the required product is obtained, and the weight average molecular weight of the product is M w 1×10 5 ~2×10 5 .
PUM
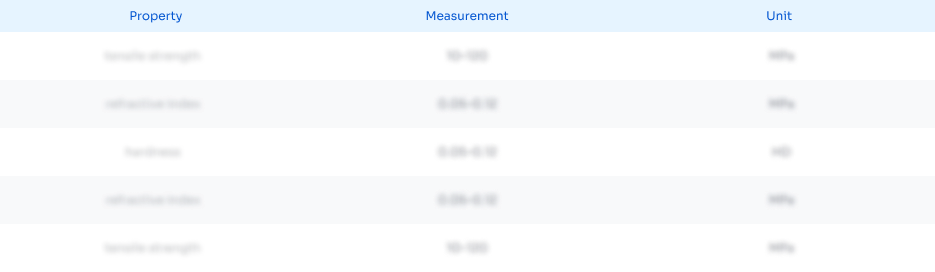
Abstract
Description
Claims
Application Information

- R&D
- Intellectual Property
- Life Sciences
- Materials
- Tech Scout
- Unparalleled Data Quality
- Higher Quality Content
- 60% Fewer Hallucinations
Browse by: Latest US Patents, China's latest patents, Technical Efficacy Thesaurus, Application Domain, Technology Topic, Popular Technical Reports.
© 2025 PatSnap. All rights reserved.Legal|Privacy policy|Modern Slavery Act Transparency Statement|Sitemap|About US| Contact US: help@patsnap.com