High conductive polyamide/graphite nano conductive composite material and preparation method thereof
A nano-conductive and high-conductivity technology, applied in the field of nano-conductive composite material preparation, can solve the problems of low filler content, complex process, unfavorable application, etc., and achieve the effects of excellent processing performance, advanced technology and broad industrialization prospects.
- Summary
- Abstract
- Description
- Claims
- Application Information
AI Technical Summary
Problems solved by technology
Method used
Image
Examples
Embodiment 1
[0018] Add natural flake graphite (30-200 mesh) into the mixture of concentrated sulfuric acid and concentrated nitric acid (mass ratio: 4:1) and soak for 24 hours. Heat treatment to obtain expanded graphite with an expansion ratio of 200-400 times. Take 9.9 grams of nylon 6 resin and add it to 200 ml of formic acid. After it is completely dissolved, add 0.1 grams of the above-mentioned graphite and ultrasonically 2 hours to obtain a uniformly dispersed mixture. Then add 200 ml of deionized water as a precipitant to precipitate the dispersed mixture. The precipitate was suction-filtered, washed with water, and dried to prepare a high-conductivity polyamide / graphite nano-conductive composite material containing 1 wt% of EG. The electrical conductivity and notched impact strength data of the obtained composites are shown in Fig. 1 and Fig. 2 .
Embodiment 2
[0020] The implementation steps are the same as in Example 1, the nylon 6 resin consumption is 9.8 grams, and the expanded graphite is 0.2 grams. The electrical conductivity and notched impact strength data of the obtained composites are shown in Fig. 1 and Fig. 2 .
Embodiment 3
[0022] Implementation steps are the same as in Example 1, the consumption of nylon 6 resin is 9.2 grams, and the expanded graphite is 0.8 grams. The electrical conductivity and notched impact strength data of the obtained composites are shown in Fig. 1 and Fig. 2 .
[0023] When the polyamide resin is nylon 66 or nylon 1010, nylon 11, nylon 12, nylon 46, nylon 610, nylon 612, nylon 1212, or aromatic nylon, a highly conductive polyamide / graphite nanoconductive composite material can also be prepared.
[0024] When the solvent is formic acid, m-cresol, dimethylformamide, trifluoroethanol, α-cyanohydrin, methanol-calcium chloride, hexamethylphosphoric triamide, 1:1 phenol-tetrachloroethane, the same A highly conductive polyamide / graphite nanoconductive composite material was prepared.
PUM
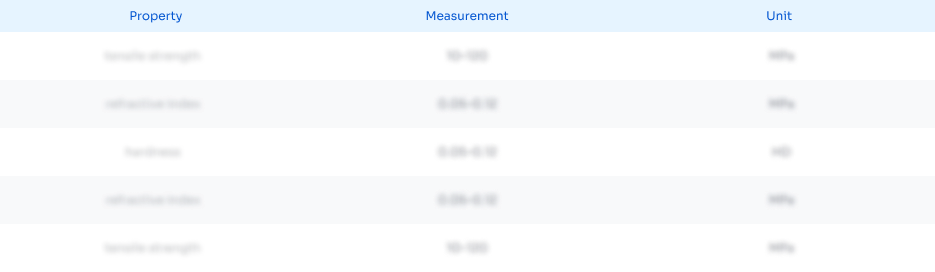
Abstract
Description
Claims
Application Information

- R&D Engineer
- R&D Manager
- IP Professional
- Industry Leading Data Capabilities
- Powerful AI technology
- Patent DNA Extraction
Browse by: Latest US Patents, China's latest patents, Technical Efficacy Thesaurus, Application Domain, Technology Topic, Popular Technical Reports.
© 2024 PatSnap. All rights reserved.Legal|Privacy policy|Modern Slavery Act Transparency Statement|Sitemap|About US| Contact US: help@patsnap.com